In the modern industry, ultra-fine powder has been unknowingly integrated into it. For example, papermaking, paper sizing is generally added with 10%-20% ultrafine powder. In copper paper, kaolin (or calcium carbonate) is superfine. The amount of powder added is as high as 40%. Another example is the plastic product, the amount of modified ultrafine powder can be as high as 30%-50% depending on the product requirements. In addition, ultrafine powders are used in plastics, rubber, electronics, cables, paints, coatings, abrasives, pharmaceuticals, cosmetics, ceramics, building materials, food processing and household appliances. For example, the production of flour in the United States requires a certain amount of talcum powder. Adding amount; adding ultrafine powder of 6000 mesh or more to plastic products can not only improve the physical indexes such as appearance size, smoothness, color and feel of the product, but also improve the strength, elasticity, toughness and anti-aging ability of the product. The ultra-fine powder processing has high requirements on fineness, and it is a challenge to the processing technology of ultra-fine powder processing equipment-superfine mill.
Clirik’s mills for various materials such as talc can accept non-flammable and explosive materials with a Mohs hardness of less than 6 mm and a Mohs hardness of 6. The crushed raw materials are mainly composed of crushed calcite, gypsum, talc, feldspar, barite, kaolin and other materials. Due to the large changes in the grinding roller and the grinding roller assembly of the main machine, the material has to go through many times from top to bottom. Grinding makes full use of the centrifugal force of the grinding roller and has a large contact area with the grinding ring, so that a high-fineness powder having a fineness of 5 to 45 μm can be produced. Its design changes the structure of the traditional mill, the grinding roller and the grinding ring are made of hard alloy, the service life is greatly extended, and it is not necessary to change the wearing parts frequently, which greatly improves the use efficiency. In some areas and fields, it can replace the jet mill produced by the United States and has high economic value.
The working principle of the talc European version mill is a vertical structure, with a small footprint and a complete set of components, and the main gear transmission adopts a closed gear box for stable transmission. The important parts of the mill are made of high quality steel, so the machine is durable and reliable. The grinder electrical system adopts centralized control, reasonable selection and high degree of automation. The vibrating feeder is small in size, light in weight, easy to adjust and saves electricity. The working process of the European version of the mill is as follows: After the bulk material is crushed to the required particle size by the jaw crusher, the material is sent to the storage hopper by the hoist, and then the material is evenly and quantitatively sent through the vibrating feeder. Grinding into the main machine grinding room, the powder after grinding increases with the airflow of the fan, and is classified by the classifier. The fine powder conforms to the airflow and enters the large cyclone collector through the pipeline, and is separated and collected. The valve discharge is the finished powder.
The talc Raymond mill is a high-fine milling machine that adapts to the closed loop of small and medium-sized mining, chemical, building materials, metallurgy, refractory materials, pharmaceutical, cement and other industries. It is a new type of mill that replaces the ball mill to process powder. The energy consumption has reached the national standard, ranking a high level in the country, and has been well received by users in various industries. The Raymond mill adopts the structure of similar foreign products and is updated and improved on the basis of the large Raymond mill. It has higher efficiency than the ball mill, low power consumption, small floor space and small one-time investment. In the process, the grinding roller of the Raymond mill is compacted on the grinding ring by the centrifugal force, so when the grinding roller and the grinding ring wear to a certain thickness, the yield and fineness of the finished product are not affected, thereby eliminating the centrifugation. In addition, the air-selected airflow of the Raymond mill is circulating in the fan–milling–cyclone-fan, with less dust and clean operation workshop. Less environmental pollution.
Our company is a manufacturer of talc grinding mills which can grind talc into powder with different fineness. If you are interested in our machine, you can contact us at any time. You can chat with us online or leaving messages on our website.
HOT PRODUCTS
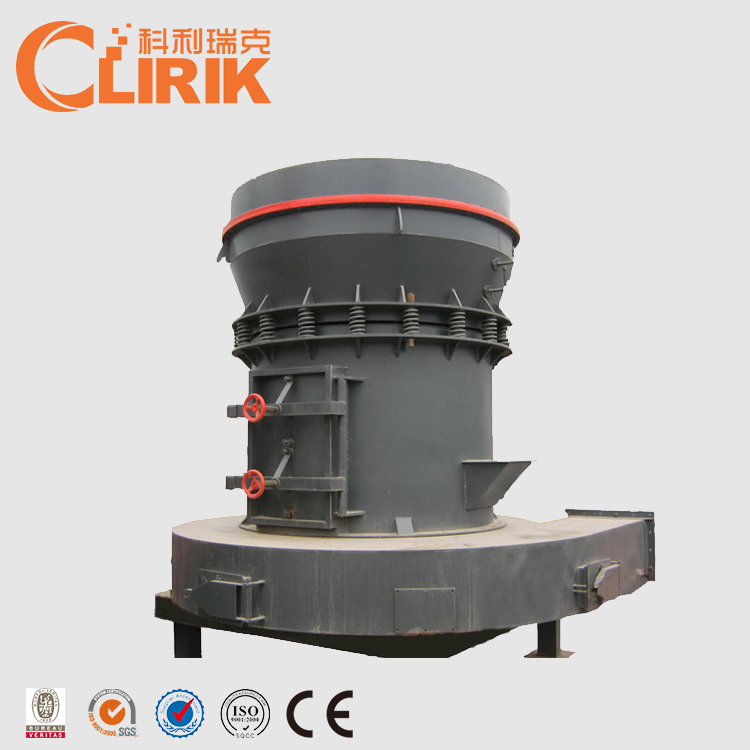
Talc Raymond Mill
Capacity: 1-25 t/h
Max feeding size: 40 mm
Discharge fineness: 50-325 mesh
Range of application: Barite, calcite, potassium feldspar, talc…… [Read More…]
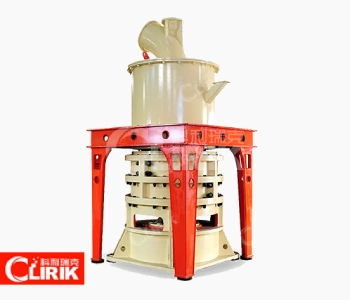
Micro Powder Grinding Mill
Capacity: 0.2-45 t/h
Max feeding size: 20 mm
Discharge fineness: 150-3000 mesh
Range of application: calcium carbonate, kaolin, carbon black, dolomite…… [Read More…]
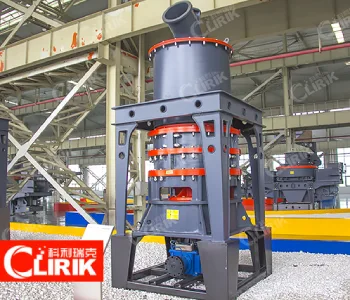
Talc Ultrafine Grinding Mill
Capacity: 0.2-45 t/h
Max feeding size: 20 mm
Discharge fineness: 150-3000 mesh
Processing materials: non-flammable and explosive non-metallic ores with Mohs hardness less than 7…… [Read More…]
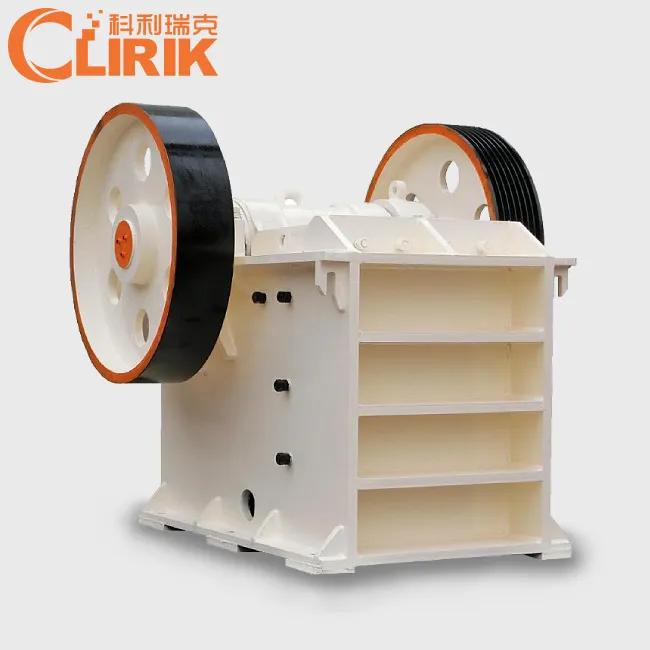
Talc Jaw Crusher
Output Size: 65-160mm
Feed size: 480mm
Capacity: 1-140t/h
Processing materials: Granite, quartz stone, river pebble, calcite, concrete, dolomite…… [Read More…]
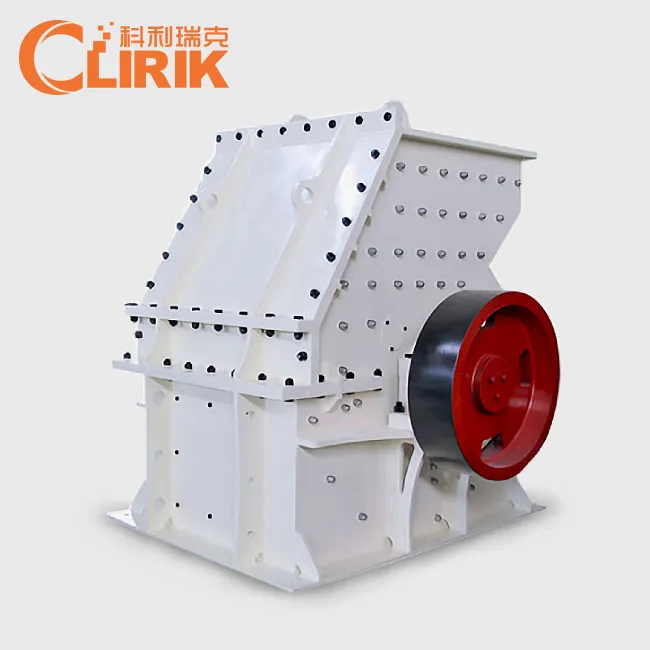
Talc Hammer Mill
Output Size: 5-20 mm
Feed size: <350 mm
Capacity: 5-30 t/h
Application: It is widely used for medium and fine crushing of brittle, medium hardness and soft materials... [Read More…]
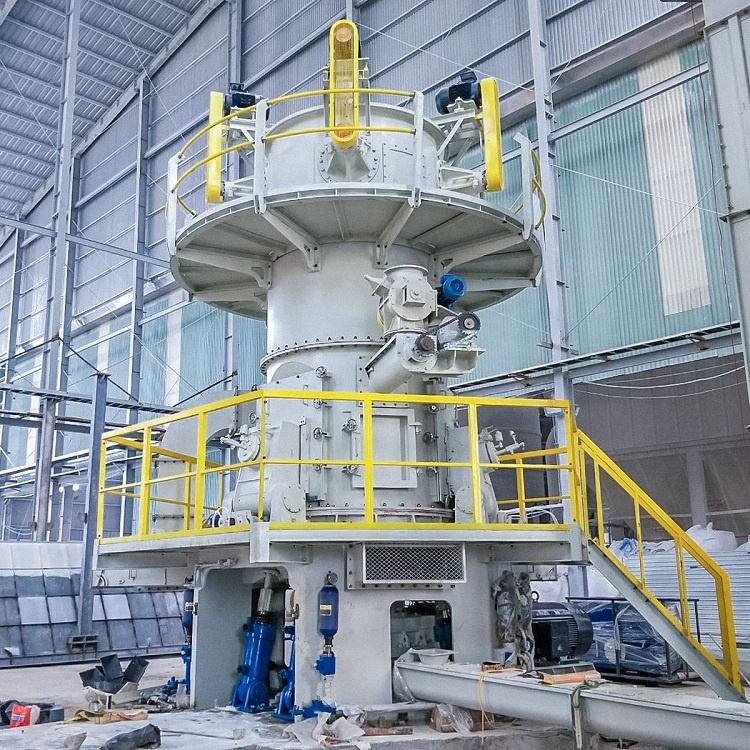
Talc Vertical Mill
Discharge fineness: 150-3000 mesh
Feed size: <15 mm
Output: 1-20 T/H
Product features: It has high grinding efficiency, low energy consumption, uniform particle shape... [Read More…]