Current stone grinding mill is generally divided into coarse powder mill and micro powder mill. Why is micro powder grinding mill applied in more fields at this moment? What has the coarse mineral powder changed after being further processed by micro powder grinding mill?
1. Changes in solubility
Such as powdered quartz, calcite, cassiterite, corundum, bauxite, chromite, magnetite, galena, titanomagnetite, volcanic ash, kaolin, etc. after being finely ground or ultra-finely ground and dissolved in inorganic acid Speed and solubility have increased.
2. Changes in sintering performance
There are two main changes in the thermal properties of materials due to fine grinding or ultra-fine grinding: First, because the dispersion of the material increases, the solid phase reaction becomes easier, the sintering temperature of the product decreases, and the mechanical properties of the product are also improved. . For example, after dolomite is finely ground in a vibrating mill, the sintering temperature for preparing refractory materials with it is reduced by 375-573K, and the mechanical properties of the material are improved. Ultrafine grinding of quartz and feldspar can shorten the sintering of enamel. The fine grinding of porcelain clay improves the strength of ceramic products. The second is that the change of crystal structure and amorphization lead to the shift of crystal phase transition temperature. For example, the transition temperature of α quartz to β quartz and cristobalite and the transition temperature of calcite to aragonite are changed by ultrafine grinding.
3. Changes in cation exchange capacity
Some silicate minerals, especially some clay minerals such as bentonite and kaolin, have significant changes in cation exchange capacity after fine grinding or ultrafine grinding. For example, with the extension of the grinding time, the ion exchange capacity of bentonite first increases and then decreases, while the calcium ion exchange capacity continues to decrease with the extension of the grinding time. After a certain period of grinding, the ion exchange capacity and displacement capacity of kaolin have been improved, indicating that the number of exchangeable cations has increased. In addition to bentonite, kaolin, and zeolite, the ion exchange capacity of other such as talc, refractory clay, mica, etc. also changes to different degrees after fine grinding or ultrafine grinding.
4. Changes in hydration performance and reactivity
The reactivity of calcium hydroxide materials can be improved by fine grinding, which is very important in the preparation of building materials. Because these materials are inert or not active enough for hydration. For example, the hydration activity of pozzolan and the reactivity with calcium hydroxide are almost zero at the beginning, but after being finely ground in a ball mill or vibration mill, it can be increased to almost the same as diatomaceous earth. Fine grinding can greatly improve the hydration performance of blast furnace waste slag. Therefore, it is possible to produce cement with high strength and more slag through fine grinding or ultra-fine grinding. This is of great significance to the cement industry and environmental protection.
5. Electrical changes
Fine grinding or ultra-fine grinding also affects the surface electrical and dielectric properties of minerals. For example, after impact crushing and grinding of biotite, its isoelectric point and surface electrokinetic potential (Zeta potential) all change.
6. Changes in density
After grinding natural zeolite (mainly composed of clinoptilolite, mordenite, and quartz) and synthetic zeolite (mainly mordenite) in a planetary ball mill, it was found that the density of the two zeolites changed differently. Studies have shown that as the grinding progresses, the density of natural zeolite decreases at the beginning and reaches a minimum at about 120 minutes. After that, it increases slightly with the extension of grinding time, but it is still lower than the original ore; synthetic zeolite decreases in a short time. After the density drops, as the grinding time increases, the density increases. After 240 minutes of grinding, the density value of the sample is higher than that of the unpolished sample.
HOT PRODUCTS
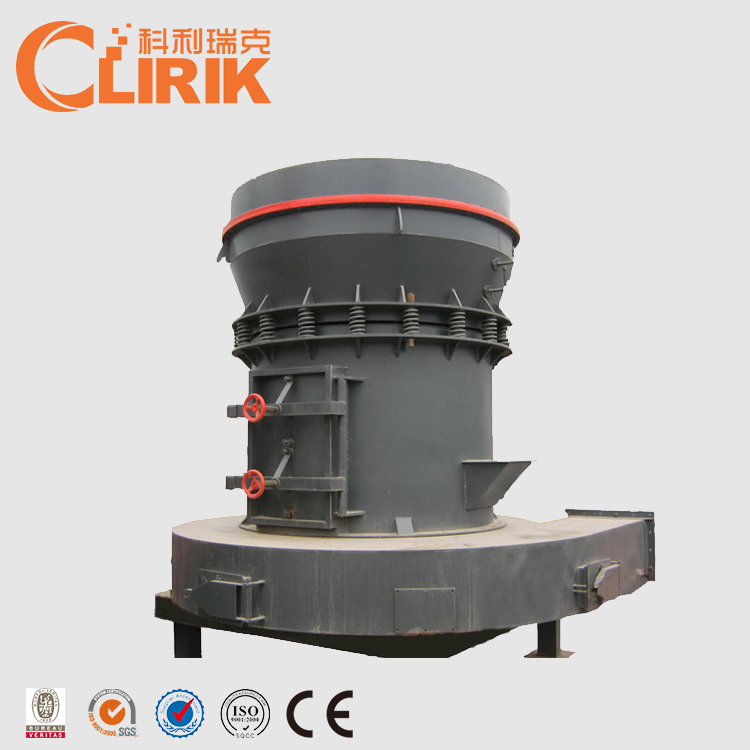
Talc Raymond Mill
Capacity: 1-25 t/h
Max feeding size: 40 mm
Discharge fineness: 50-325 mesh
Range of application: Barite, calcite, potassium feldspar, talc…… [Read More…]
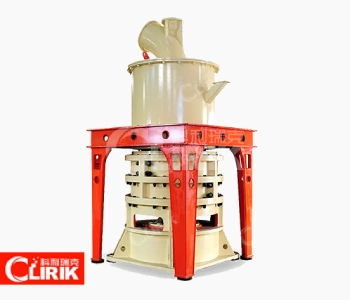
Micro Powder Grinding Mill
Capacity: 0.2-45 t/h
Max feeding size: 20 mm
Discharge fineness: 150-3000 mesh
Range of application: calcium carbonate, kaolin, carbon black, dolomite…… [Read More…]
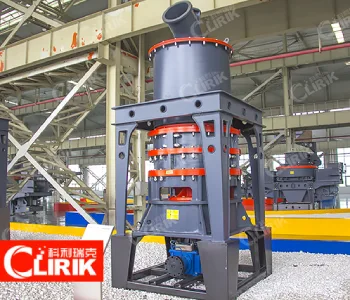
Talc Ultrafine Grinding Mill
Capacity: 0.2-45 t/h
Max feeding size: 20 mm
Discharge fineness: 150-3000 mesh
Processing materials: non-flammable and explosive non-metallic ores with Mohs hardness less than 7…… [Read More…]
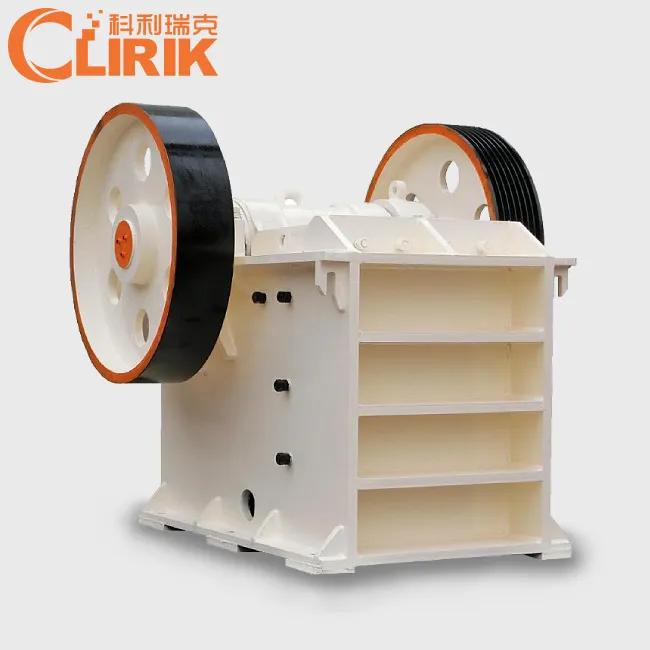
Talc Jaw Crusher
Output Size: 65-160mm
Feed size: 480mm
Capacity: 1-140t/h
Processing materials: Granite, quartz stone, river pebble, calcite, concrete, dolomite…… [Read More…]
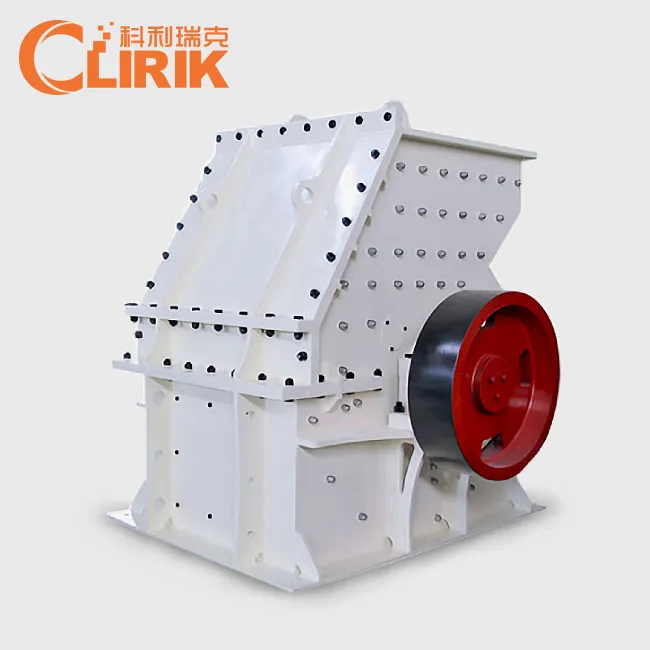
Talc Hammer Mill
Output Size: 5-20 mm
Feed size: <350 mm
Capacity: 5-30 t/h
Application: It is widely used for medium and fine crushing of brittle, medium hardness and soft materials... [Read More…]
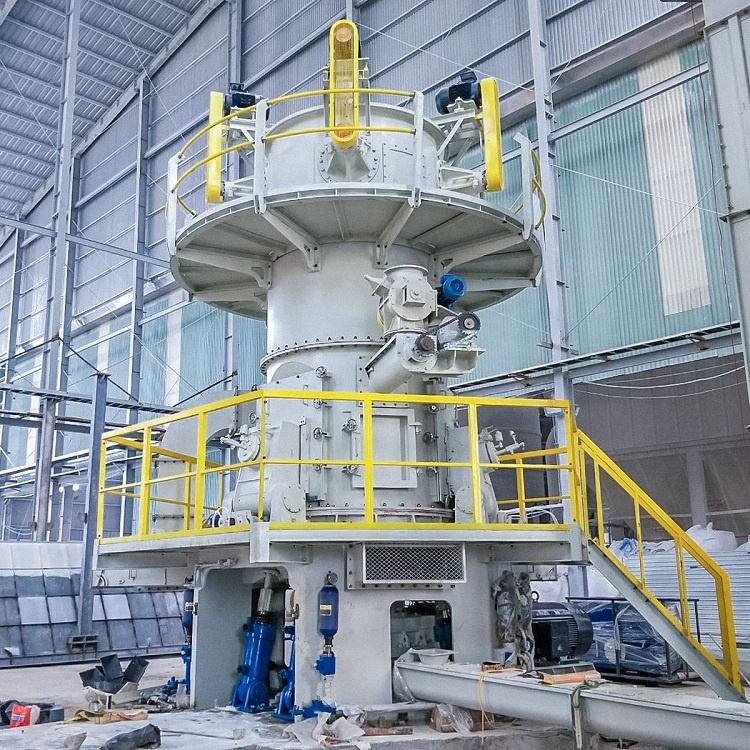
Talc Vertical Mill
Discharge fineness: 150-3000 mesh
Feed size: <15 mm
Output: 1-20 T/H
Product features: It has high grinding efficiency, low energy consumption, uniform particle shape... [Read More…]