Limestone is a kind of stone widely found in nature. Its main component is calcium carbonate. Limestone can be directly processed into stone using crushing equipment and fired into quicklime. Quicklime absorbs moisture or adds water to become hydrated lime. The main component of hydrated lime is calcium hydroxide. The hydrated lime is prepared into lime slurry, lime paste, etc., which are used as coating materials and brick adhesives.
According to the characteristics of limestone materials, several machines that are often configured in limestone production lines are recommended: jaw crusher, impact crusher, screening feeding and other supporting equipment.
1. Primary crushing selection-jaw crushing
Large pieces of limestone need to be transported into the jaw crusher by the feeder for preliminary crushing, and the crushed materials will be transported to the next stage;
2. Secondary crushing option-counterattack crushing
The coarsely crushed limestone is sent to the impact crusher by the conveyor for further crushing. The impact crusher has good wear resistance, good discharge particle size, and low content of fine materials and stone powder.
3. Screening selection-vibrating screen
The finely crushed stone material after impact crushing enters the vibrating screen to screen out stone specifications that meet production needs.
4. Return material broken
The limestone that does not meet the specifications screened out by the screening machine must be returned to the impact crusher for crushing again until it meets the requirements of the finished product specifications.
Limestone crushing production line production configuration
The limestone crushing production line mainly consists of vibrating feeder, jaw crusher, impact crusher, vibrating screen, belt conveyor, centralized electronic control and other equipment; in order to meet the different processing needs of customers, it can be equipped with cone crusher, dust collector Equipment etc. Jaw crusher coarsely crushes sand and gravel with strong feeding force; impact crusher finely crushes sand and gravel with small size and low energy consumption; cone crusher finely crushes high hardness with strong crushing force and high safety factor; sand making machine processing capacity Strong, uniform grain shape.
1. Feeding stage: Vibrating feeders are commonly used, which can feed materials into the crusher evenly, quantitatively, and continuously.
2. Crushing stage: The crushing process involves several crushers, mainly coarse crushing and medium and fine crushing equipment. Jaw crushers are mainly used for coarse crushing, and cone crushers and impact crushers are mainly used for medium and fine crushing equipment. Whether it is hard rocks such as granite or soft rocks such as limestone, they can be processed.
3. Sand making stage: The sand making stage is generally used after the crushing stage. Vertical shaft impact crusher is commonly used, which can further finely crush and shape the stones produced by the crushing process to produce machine-made sand specifications below 5mm.
4. Screening stage: The screening operation is an auxiliary process. The finished sand and gravel materials from crushing or sand making processing are screened through the vibrating screen to obtain the required finished product specifications and gradations.
5. Conveying stage: Conveying and screening are also auxiliary processes. Belt conveyor is an ideal and efficient continuous conveying equipment, which has the characteristics of continuous conveying, reliability and convenience, long conveying distance, low energy consumption, large conveying capacity, green and environmental protection.
6. Sand washing and dust removal stage: Generally, dust removal equipment and sand washing equipment are configured as needed. Under the requirements of environmental protection, dust pollution is minimized. The sand washing machine is generally equipped with a wheel sand washing machine, which has high output, simple operation, and convenient operation.
HOT PRODUCTS
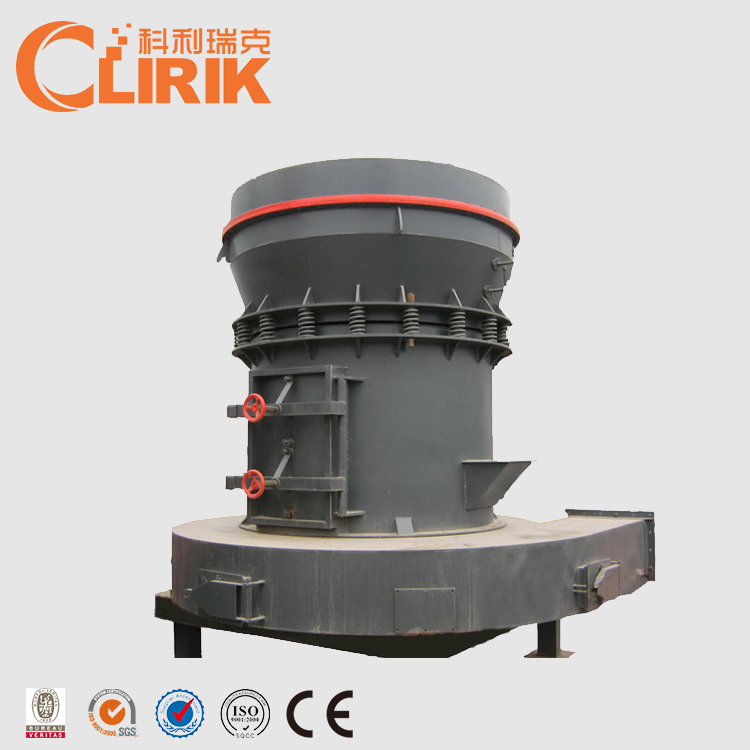
Talc Raymond Mill
Capacity: 1-25 t/h
Max feeding size: 40 mm
Discharge fineness: 50-325 mesh
Range of application: Barite, calcite, potassium feldspar, talc…… [Read More…]
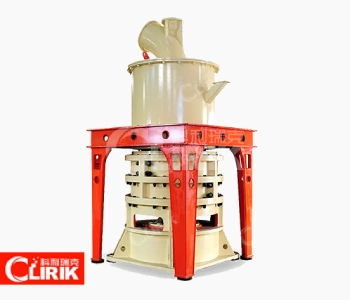
Micro Powder Grinding Mill
Capacity: 0.2-45 t/h
Max feeding size: 20 mm
Discharge fineness: 150-3000 mesh
Range of application: calcium carbonate, kaolin, carbon black, dolomite…… [Read More…]
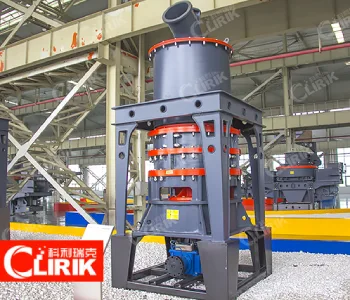
Talc Ultrafine Grinding Mill
Capacity: 0.2-45 t/h
Max feeding size: 20 mm
Discharge fineness: 150-3000 mesh
Processing materials: non-flammable and explosive non-metallic ores with Mohs hardness less than 7…… [Read More…]
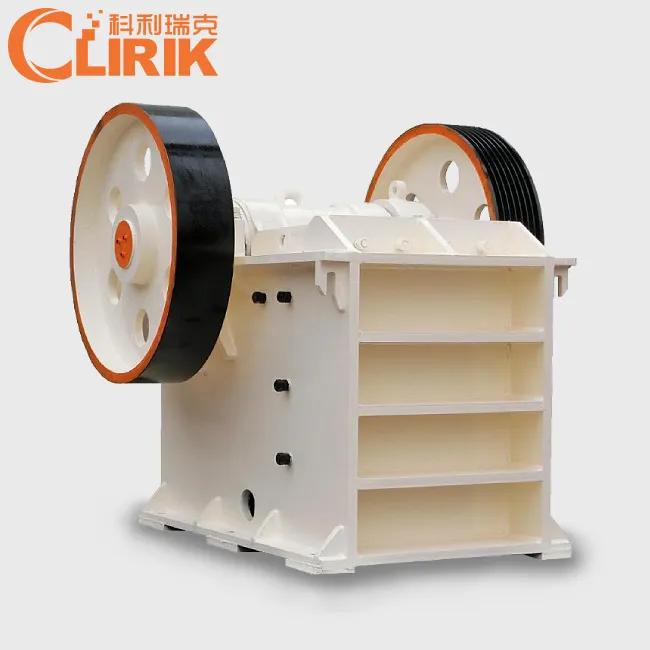
Talc Jaw Crusher
Output Size: 65-160mm
Feed size: 480mm
Capacity: 1-140t/h
Processing materials: Granite, quartz stone, river pebble, calcite, concrete, dolomite…… [Read More…]
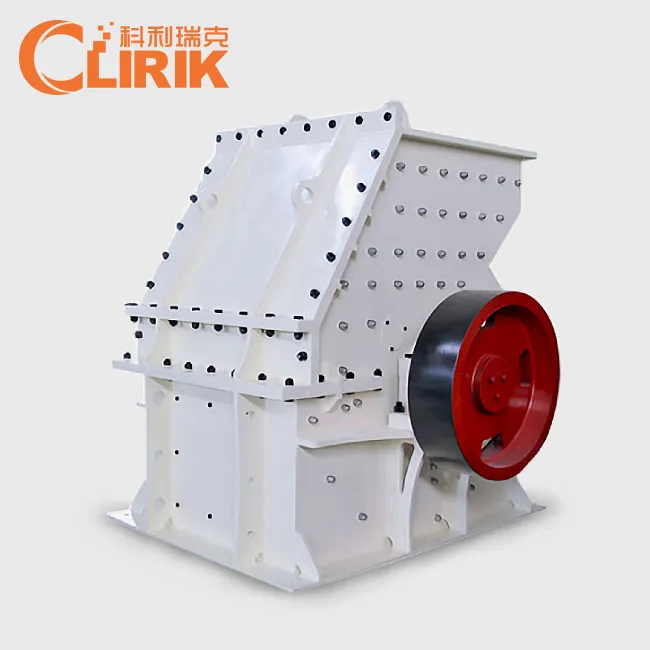
Talc Hammer Mill
Output Size: 5-20 mm
Feed size: <350 mm
Capacity: 5-30 t/h
Application: It is widely used for medium and fine crushing of brittle, medium hardness and soft materials... [Read More…]
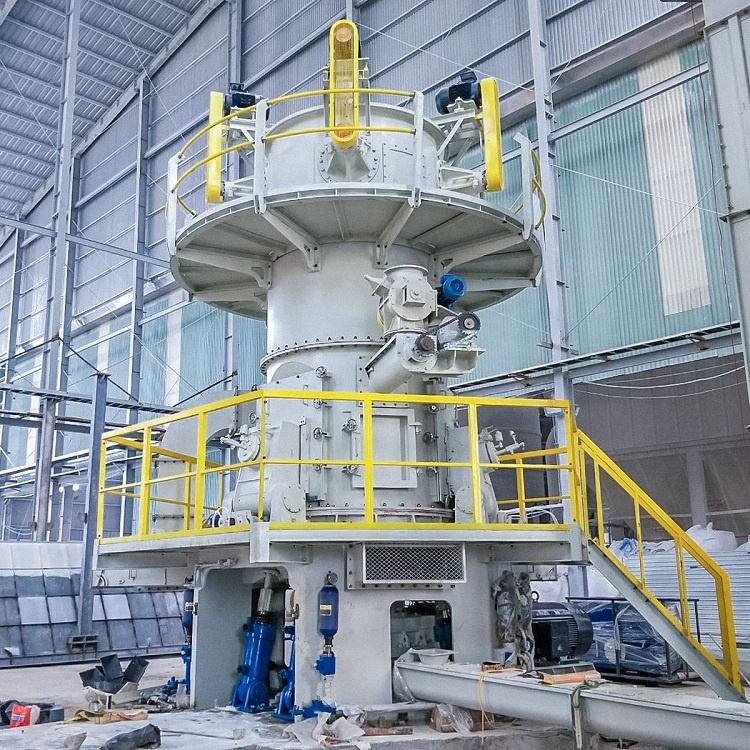
Talc Vertical Mill
Discharge fineness: 150-3000 mesh
Feed size: <15 mm
Output: 1-20 T/H
Product features: It has high grinding efficiency, low energy consumption, uniform particle shape... [Read More…]