At present, almost all general-purpose plastics can be used for 3D printing, but due to the differences in the characteristics of each plastic, the 3D printing process and product performance are affected.
The main factors affecting the application of plastic materials in 3D printing are: high printing temperature and poor material fluidity, which leads to volatile components in the working environment; print nozzles are easy to block, affecting the precision of products; ordinary plastics have low strength and the scope of adaptation is too narrow , then it need to do enhanced treatment of plastic; poor cooling uniformity, slow shaping, easy to cause product shrinkage and deformation; lack of functional and intelligent applications.
To this end, the development of 3D printing plastic modification technology currently has the following four directions.
- Liquidity modification
In order to achieve flow modification of plastics, lubricants, etc. can be used. However, the use of too much lubricant will increase the volatile content and weaken the rigidity and strength of the product. Therefore, by adding high-rigidity, high-fluidity spherical barium sulfate, glass beads, and other inorganic materials, it can make up for the defects of poor plastic fluidity. For powder plastics, powder inorganic powder such as talc powder, mica powder, etc. can be coated on the powder surface to increase the fluidity. In addition, microspheres can be directly formed during plastic synthesis to ensure fluidity.
- Enhanced modification
The rigidity and strength of plastics can be improved by reinforcing materials. For example, the reinforcement of ABS through glass fiber, metal fiber and wood fiber makes the composite material suitable for 3D fused deposition process; powdered plastic is usually sintered by laser, which can be modified by compounding multiple materials, including the addition of glass fiber Nylon powder, nylon powder with carbon fiber added, nylon mixed with polyetherketone, etc.
- Rapid solidification
The solidification time of plastics is closely related to crystallinity. In order to accelerate the rapid solidification of plastics after 3D fused deposition, you can use reasonable nucleating agents to accelerate the plastic solidification and solidification, or you can compound metals with different heat capacities in the plastic material to accelerate the solidification speed.
4. Functionalization
The use of plastic materials for 3D printing is restricted in some areas due to the particularity of the materials. But if plastics are given some functions, it will greatly expand the scope of plastics in the field of 3D printing manufacturing.
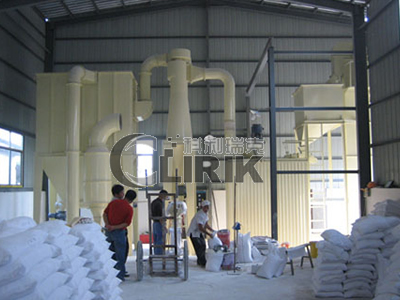
We produce talc grinding mill and talcum powder surface modification machine. For people who requires talc powder no more than 3000 mesh, we can absolutely reach that needs. More information can be sent to you if you are interested.
HOT PRODUCTS
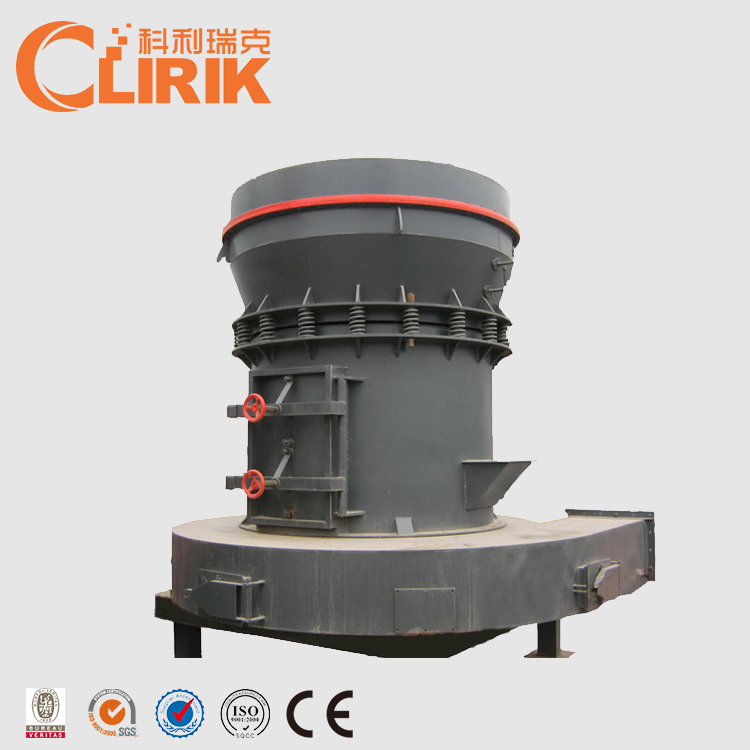
Talc Raymond Mill
Capacity: 1-25 t/h
Max feeding size: 40 mm
Discharge fineness: 50-325 mesh
Range of application: Barite, calcite, potassium feldspar, talc…… [Read More…]
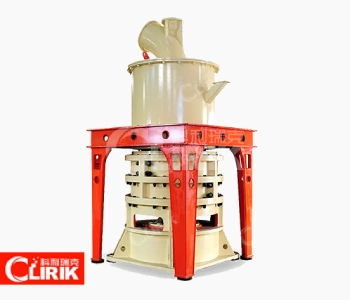
Micro Powder Grinding Mill
Capacity: 0.2-45 t/h
Max feeding size: 20 mm
Discharge fineness: 150-3000 mesh
Range of application: calcium carbonate, kaolin, carbon black, dolomite…… [Read More…]
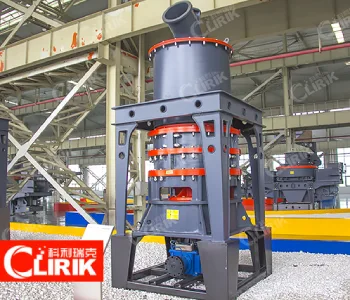
Talc Ultrafine Grinding Mill
Capacity: 0.2-45 t/h
Max feeding size: 20 mm
Discharge fineness: 150-3000 mesh
Processing materials: non-flammable and explosive non-metallic ores with Mohs hardness less than 7…… [Read More…]
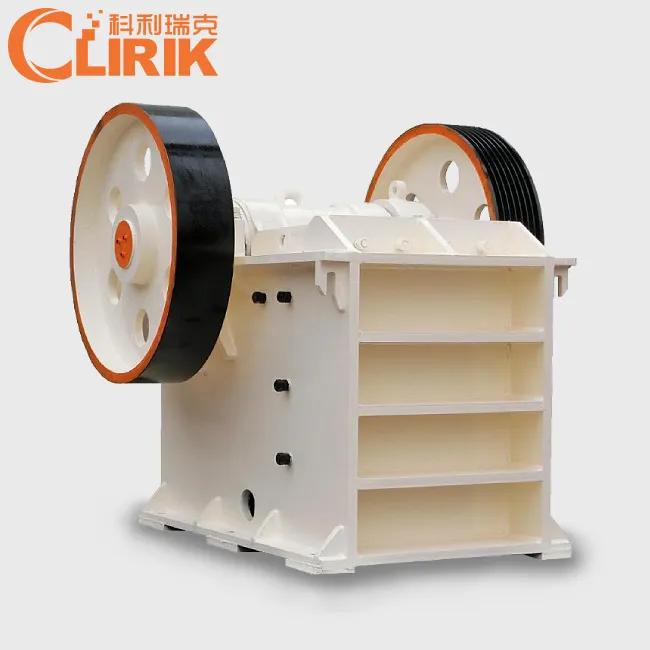
Talc Jaw Crusher
Output Size: 65-160mm
Feed size: 480mm
Capacity: 1-140t/h
Processing materials: Granite, quartz stone, river pebble, calcite, concrete, dolomite…… [Read More…]
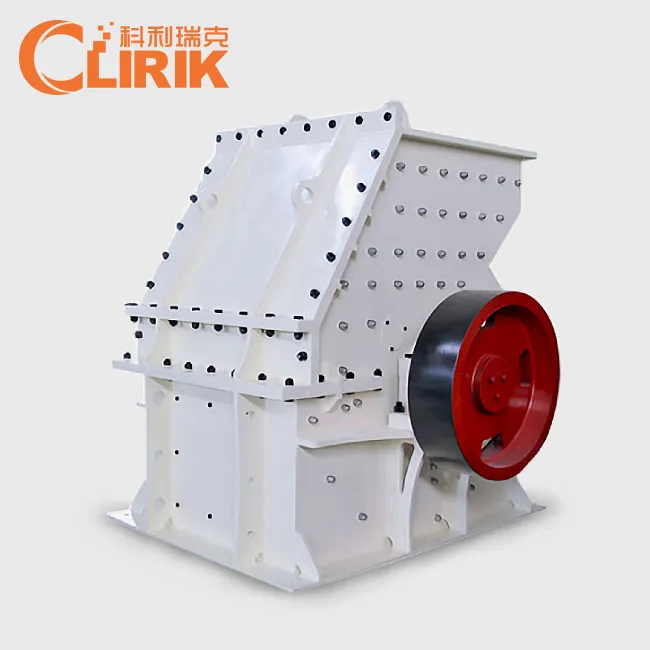
Talc Hammer Mill
Output Size: 5-20 mm
Feed size: <350 mm
Capacity: 5-30 t/h
Application: It is widely used for medium and fine crushing of brittle, medium hardness and soft materials... [Read More…]
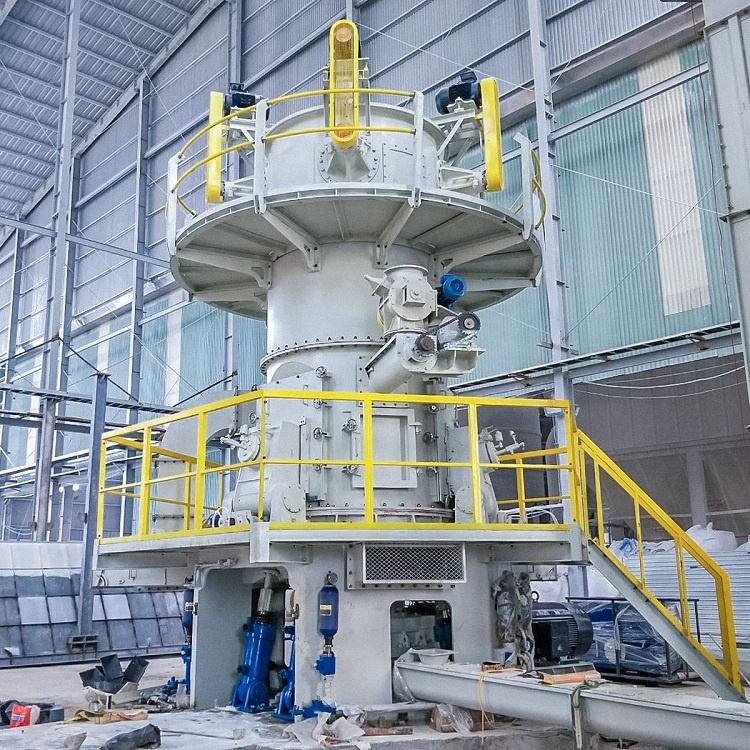
Talc Vertical Mill
Discharge fineness: 150-3000 mesh
Feed size: <15 mm
Output: 1-20 T/H
Product features: It has high grinding efficiency, low energy consumption, uniform particle shape... [Read More…]