Nowadays, powder technology has been developed in the direction of nanometer and narrow particle size distribution. However, due to the large surface area and high surface energy of ultrafine powder, powder particles will attract each other, which will easily cause powder. Agglomeration, which seriously affects the performance of the product, therefore, the problem of dispersion has become a key core technology in the research of ultrafine powders.
According to the cause of powder agglomeration, the powder agglomeration phenomenon can be roughly divided into two categories: soft agglomeration and hard agglomeration. The soft agglomeration of the powder is formed by the electrostatic force and van der Waals force between the powder particles, and it is easier to disperse; and the hard agglomeration has been studied by many scientific workers, it is mainly formed by chemical bonding, so it is difficult to disperse.
In view of the agglomeration phenomenon of ultrafine powders, the powder dispersion methods can be divided into two categories: physical dispersion methods and chemical dispersion methods. The physical dispersion method mainly solves the hard agglomeration of the powder, mainly including: ultrasonic dispersion method, mechanical dispersion method, electrostatic dispersion method, and dry dispersion method. The chemical dispersion has obviously improved the soft agglomeration of the powder, and the methods mainly include: dispersant method and surface modification method.
In general, although the ultrasonic method can be used to disperse ultrafine powders, the dispersion effect can be obtained, but the dispersion stability of the dispersion is mostly poor, and the energy consumption of ultrasonic dispersion is large, which is not easy to apply on a large scale due to cost , Currently only used in the laboratory. The mechanical dispersion method is one of the most commonly used ultrafine powder dispersion methods due to its simple operation and low cost. However, it also has some significant shortcomings. For example, the biggest disadvantage of the ball milling method is that during the grinding process, the severe impact between the material, the ball and the ball mill tank causes great wear, and the worn material enters the slurry and It becomes difficult to remove impurities, which adversely affects the purity of the slurry. In addition, in some specific cases, the ball milling process can also change the physicochemical properties of the powder. For example, increasing lattice imperfections, forming a surface amorphous layer, and the like.
Therefore, a single physical dispersion will always be subject to various restrictions in the application and cannot achieve the desired dispersion effect. In general, chemical methods are also required to achieve better dispersion in practical applications. There are two main ways to chemically disperse powder particles. One is to add a dispersant to the suspension. The mechanism of dispersant promoting particle dispersion is that it adsorbs on the surface of powder particles, improves the compatibility between particles and medium, thereby changing the interaction between particles and medium, particles and particles, increasing the repulsive force between particles, and hindering Agglomeration between particles. When using a dispersant, it is necessary to pay attention to the type, amount, and addition method of the dispersant. The other is surface modification of the powder particles, and organic molecules having good compatibility with the liquid phase solvent are grafted on the surface of the powder particles through chemical reactions to change the surface properties of the powder and achieve a stable dispersion effect. Compared to physical methods, chemical methods generally have better dispersion stability. In actual production, physical methods and chemical methods are often used in combination. Physical methods are used to de-aggregate, and then chemical methods are used to stabilize the slurry, which can achieve better dispersion effects.
Our company produces mineral powder surface coating machine( mineral powder modification machine).

HOT PRODUCTS
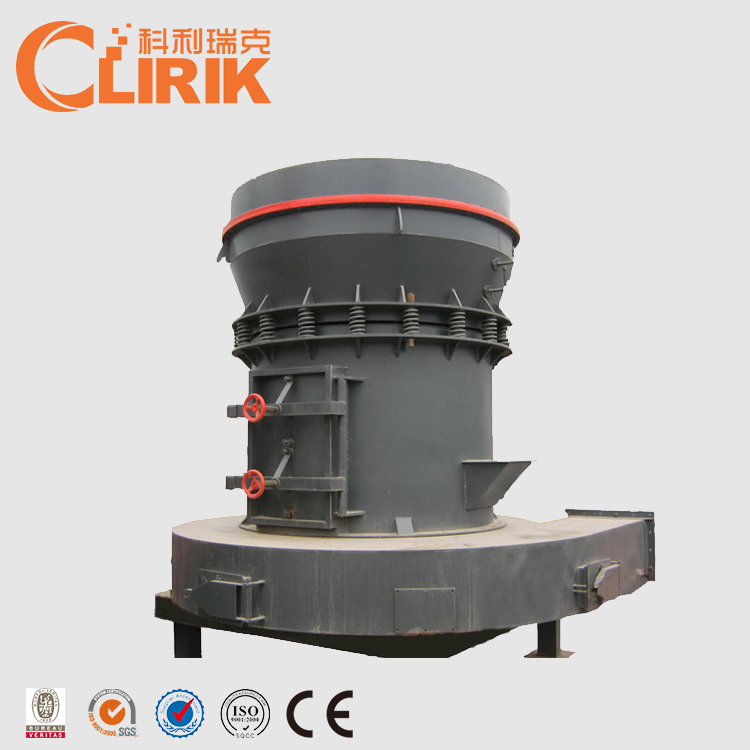
Talc Raymond Mill
Capacity: 1-25 t/h
Max feeding size: 40 mm
Discharge fineness: 50-325 mesh
Range of application: Barite, calcite, potassium feldspar, talc…… [Read More…]
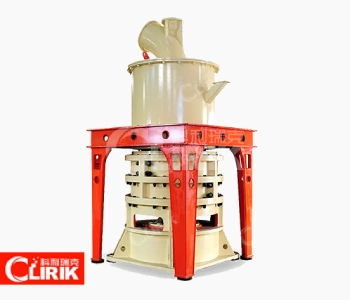
Micro Powder Grinding Mill
Capacity: 0.2-45 t/h
Max feeding size: 20 mm
Discharge fineness: 150-3000 mesh
Range of application: calcium carbonate, kaolin, carbon black, dolomite…… [Read More…]
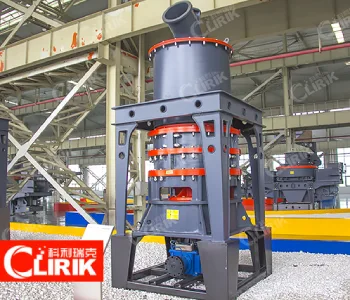
Talc Ultrafine Grinding Mill
Capacity: 0.2-45 t/h
Max feeding size: 20 mm
Discharge fineness: 150-3000 mesh
Processing materials: non-flammable and explosive non-metallic ores with Mohs hardness less than 7…… [Read More…]
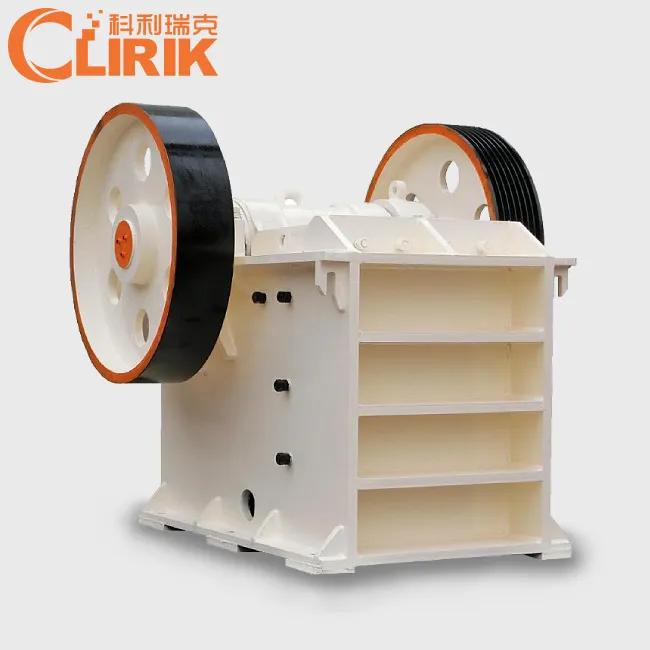
Talc Jaw Crusher
Output Size: 65-160mm
Feed size: 480mm
Capacity: 1-140t/h
Processing materials: Granite, quartz stone, river pebble, calcite, concrete, dolomite…… [Read More…]
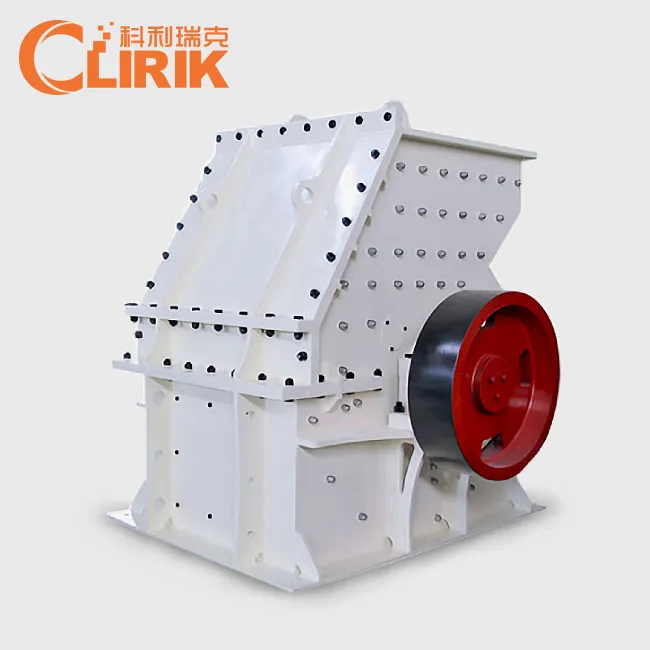
Talc Hammer Mill
Output Size: 5-20 mm
Feed size: <350 mm
Capacity: 5-30 t/h
Application: It is widely used for medium and fine crushing of brittle, medium hardness and soft materials... [Read More…]
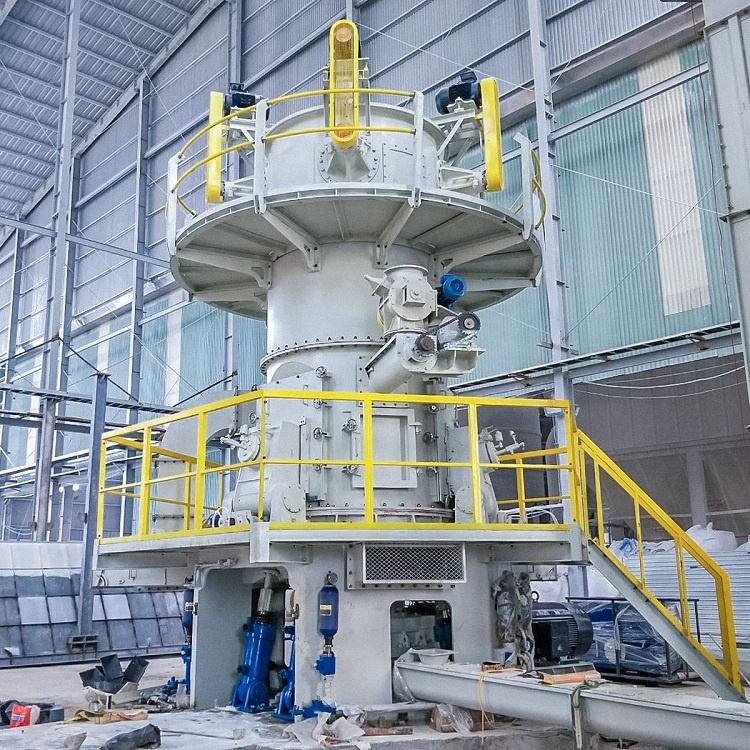
Talc Vertical Mill
Discharge fineness: 150-3000 mesh
Feed size: <15 mm
Output: 1-20 T/H
Product features: It has high grinding efficiency, low energy consumption, uniform particle shape... [Read More…]