The ultrafine calcium carbonate powder used in papermaking is obtained by grinding the raw material limestone or calcite through a grinding mill. Generally speaking, the fineness requirement of calcium carbonate powder for papermaking is 200 mesh-1250 mesh, so a multi-stage grinding process is required, and a high-fine grinding machine is used for grinding during the production process.
The production process of ultrafine calcium carbonate powder used in papermaking is mainly divided into several steps such as raw material preparation, crushing, grinding, grading, drying, and packaging.
Raw material preparation
The raw material of ultrafine calcium carbonate powder for papermaking is generally limestone or calcite, which has high quality requirements and should have the characteristics of high whiteness, few impurities, and moderate hardness. After the raw materials are crushed and screened, coarse powder is obtained.
Broken
The coarse powder is broken into small particles by the crusher for easy grinding. The choice of crusher should be determined based on the hardness of the raw materials, output and other factors.
Grinding powder
The coarse powder is ground by a grinder to obtain ultrafine calcium carbonate powder. The selection of grinding mill should be determined based on factors such as finished product fineness and output. Commonly used mills include ball mills, Raymond mills, ultra-fine mills, vertical roller mills, etc.
Grading
The ultrafine calcium carbonate powder after grinding needs to be classified due to uneven particle size to obtain products that meet the requirements. Commonly used classification equipment include vibrating screens, air flow classifiers, etc.
Dry
Ultrafine calcium carbonate powder has a high moisture content and needs to be dried to reduce the moisture content and improve the fluidity and storage stability of the powder. Commonly used drying equipment includes drum dryers, fluidized bed dryers, etc.
Package
The dried ultrafine calcium carbonate powder needs to be packaged for easy transportation and storage. Commonly used packaging materials include plastic bags, paper bags, etc.
The equipment of the ultrafine calcium carbonate powder production line for papermaking mainly includes the following types:
Raw material storage bin: used to store calcium carbonate raw materials, usually limestone or calcite.
Crusher: used to crush raw materials to obtain coarse powder.
Mill: Used to grind powder to obtain ultra-fine calcium carbonate powder.
Classifier: used to classify ultrafine calcium carbonate powder to obtain products that meet the requirements.
Dryer: used to dry ultrafine calcium carbonate powder and reduce moisture content.
Packaging machine: used to package ultra-fine calcium carbonate powder for easy transportation and storage.
The equipment configuration of the specific production line should be determined based on factors such as production scale, raw material conditions, and finished product requirements.
The key equipment of the paper grade calcium carbonate production line is the grinding mill. The selection of grinding mill needs to be determined based on factors such as the hardness, fineness requirements and output of the raw materials. At present, commonly used grinding machines include Raymond mill, European version mill, micro powder mill, etc.
Raymond mill is a traditional grinding mill with the advantages of simple structure, convenient operation and low price, but its output is low and the fineness is coarse. The European version mill is an improved version of Raymond mill. It has the advantages of high output and high fineness, but its price is higher. Micro-powder mill is currently the most advanced grinding mill, with the advantages of high output, high fineness, and low energy consumption, but its price is also relatively high.
The production process of paper grade calcium carbonate production line is relatively simple, but the following points need to be noted:
Selection of raw materials: The hardness, fineness and impurity content of the raw materials will affect the fineness and performance of the powder.
Optimization of grinding process: Reasonable selection of grinding machine and grinding process according to the characteristics and fineness requirements of the raw materials.
Storage and transportation of powder: Powder should be stored in a dry, ventilated environment and protected from moisture and dust.
HOT PRODUCTS
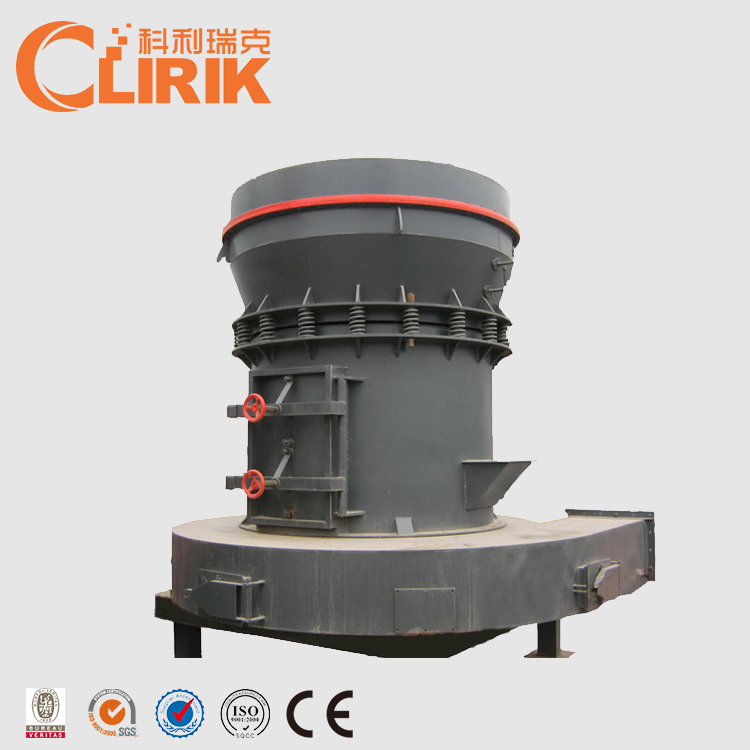
Talc Raymond Mill
Capacity: 1-25 t/h
Max feeding size: 40 mm
Discharge fineness: 50-325 mesh
Range of application: Barite, calcite, potassium feldspar, talc…… [Read More…]
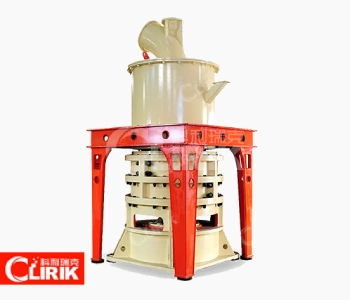
Micro Powder Grinding Mill
Capacity: 0.2-45 t/h
Max feeding size: 20 mm
Discharge fineness: 150-3000 mesh
Range of application: calcium carbonate, kaolin, carbon black, dolomite…… [Read More…]
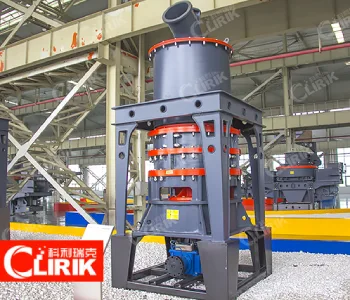
Talc Ultrafine Grinding Mill
Capacity: 0.2-45 t/h
Max feeding size: 20 mm
Discharge fineness: 150-3000 mesh
Processing materials: non-flammable and explosive non-metallic ores with Mohs hardness less than 7…… [Read More…]
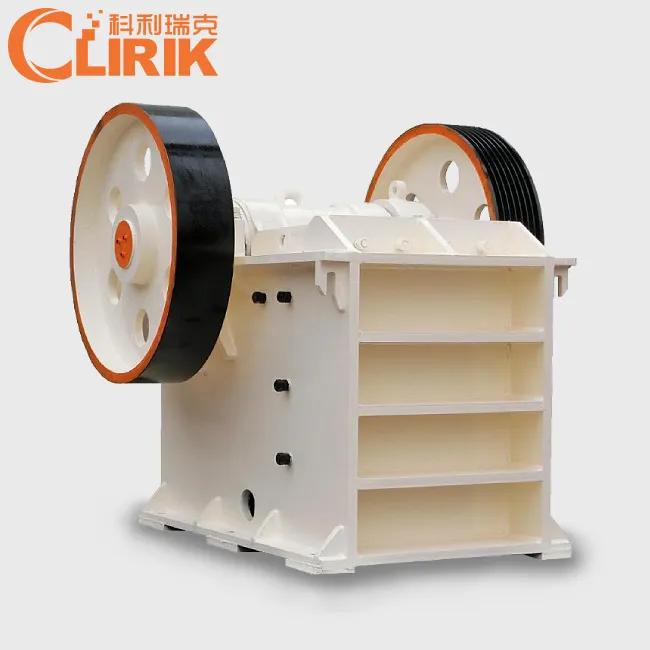
Talc Jaw Crusher
Output Size: 65-160mm
Feed size: 480mm
Capacity: 1-140t/h
Processing materials: Granite, quartz stone, river pebble, calcite, concrete, dolomite…… [Read More…]
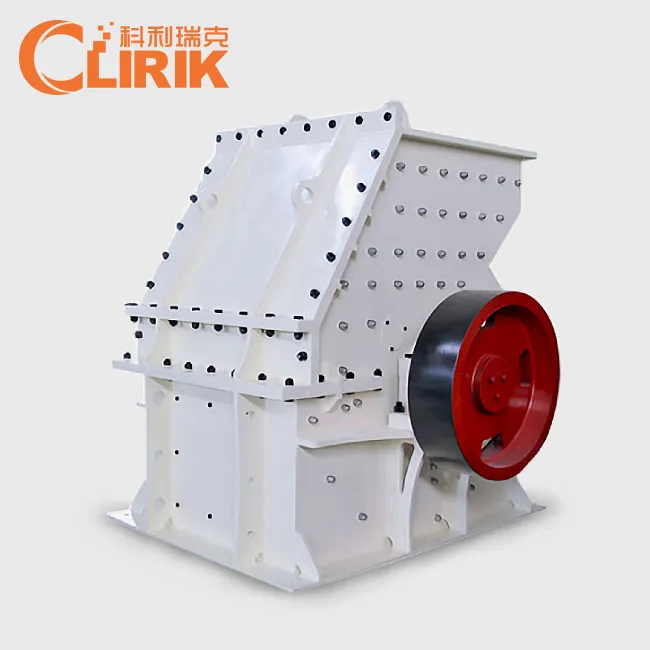
Talc Hammer Mill
Output Size: 5-20 mm
Feed size: <350 mm
Capacity: 5-30 t/h
Application: It is widely used for medium and fine crushing of brittle, medium hardness and soft materials... [Read More…]
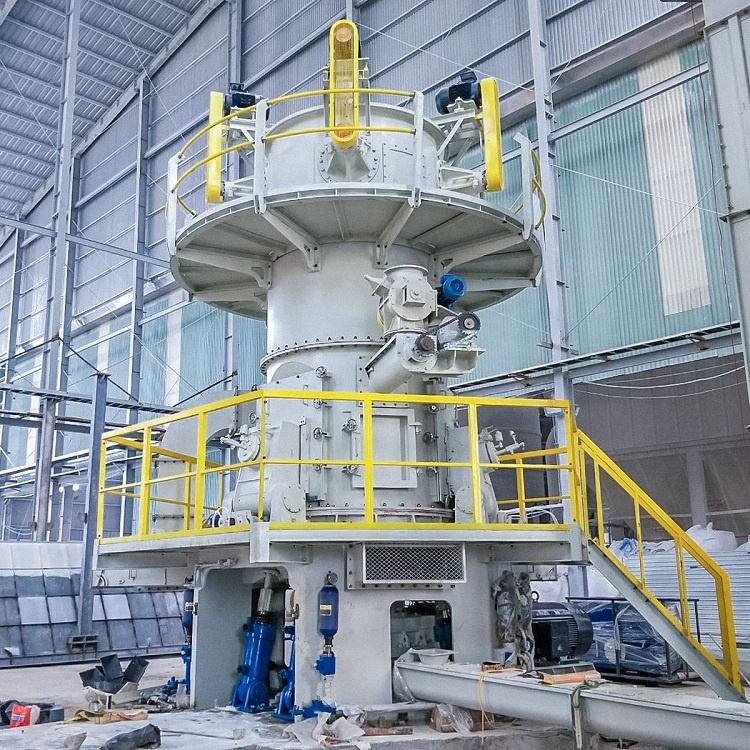
Talc Vertical Mill
Discharge fineness: 150-3000 mesh
Feed size: <15 mm
Output: 1-20 T/H
Product features: It has high grinding efficiency, low energy consumption, uniform particle shape... [Read More…]