Nowadays, due to the rapid development of the material processing industry in various industries, vertical mills have gradually become an important fine powder processing equipment in the machinery industry. The development of the powder industry has not only made great achievements in the industry, but also greatly helped our daily lives. Plastics, paints, papermaking, food and medicine, etc., are closely related to our lives, and we have lived to be so colorful is inseparable from the development of the mill industry.
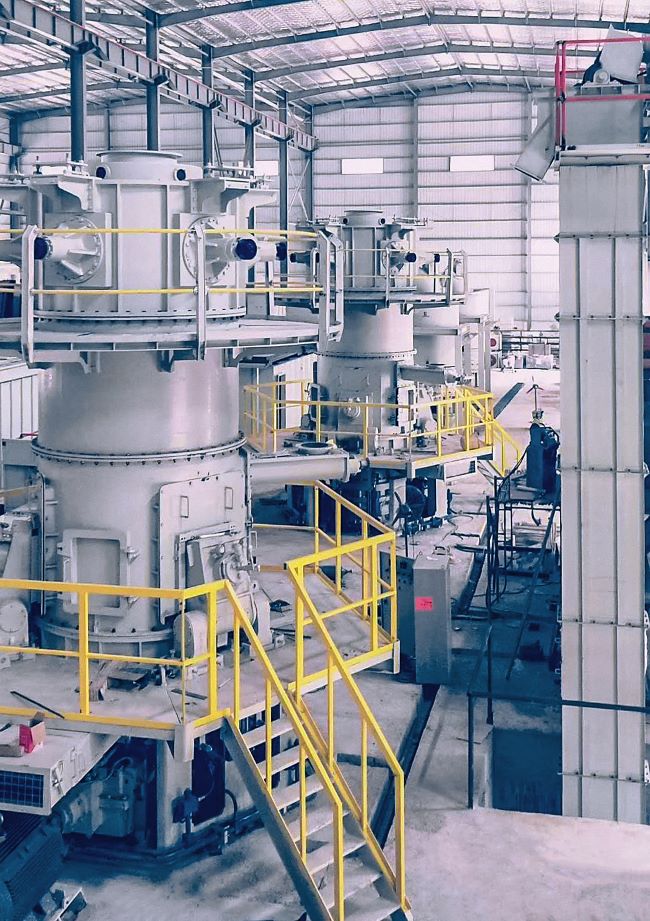
Today, I will mainly explain how often the grinding roller in the vertical mill needs to be replaced. The grinding roller is one of the vulnerable parts in the grinding equipment, because when processing materials, the main motor drives the grinding disc to rotate through the reducer when working. At the same time, hot air enters the vertical mill body from the air inlet, and the material falls in the middle of the grinding disc from the discharge port. Under the action of centrifugal force, the material moves evenly from the middle of the grinding disc to the edge. The large pieces of materials are directly crushed, and the fine-grained materials are squeezed to form a bed for inter-particle crushing. Therefore, the wear of the grinding roller is relatively common, so how often does it need to be replaced?
First of all, the grinding roller in the vertical mill depends on what material it is made of. Good materials can extend the life of the grinding roller. When processing materials, friction cannot be avoided. Over time, the grinding roller will Slowly become thinner. Therefore, generally speaking, the grinding roller needs to be replaced in time after the use time reaches 500 hours. If the replacement is not found in time, the grinding roller may be severely worn and deformed, and the particle size of the ground powder may not be passed.
Therefore, in our daily production, we must regularly check the accessories in the vertical mill. If the wearing parts are found to be severely worn, they must be replaced in time. Not only the grinding rollers, but other such as anchor nuts and shovel blades. , Bearings and other wearing parts, do a good job of timely handling of the problem. In normal times, all parts should be maintained in time to ensure the normal operation of the equipment.
HOT PRODUCTS
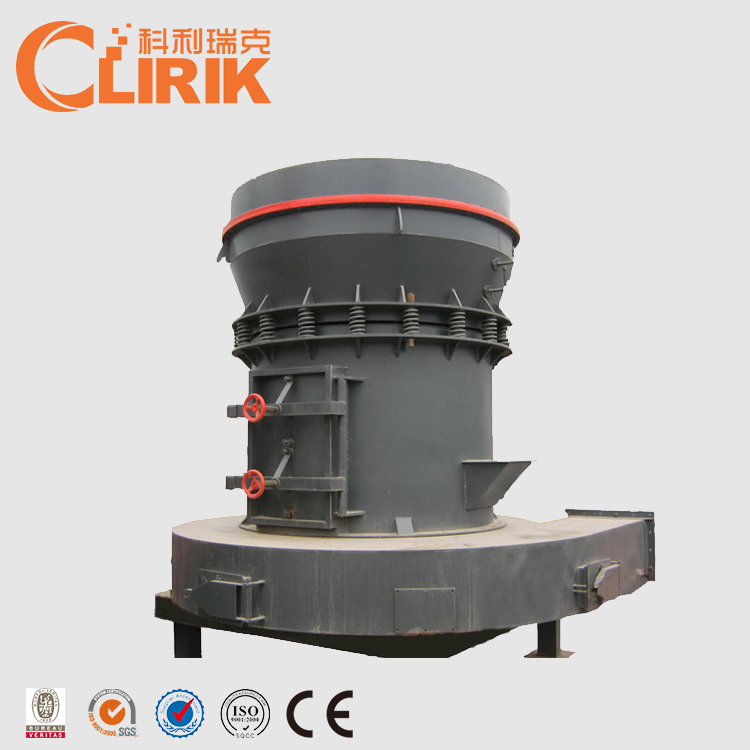
Talc Raymond Mill
Capacity: 1-25 t/h
Max feeding size: 40 mm
Discharge fineness: 50-325 mesh
Range of application: Barite, calcite, potassium feldspar, talc…… [Read More…]
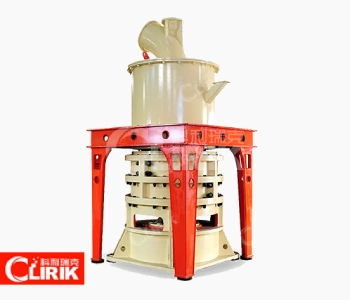
Micro Powder Grinding Mill
Capacity: 0.2-45 t/h
Max feeding size: 20 mm
Discharge fineness: 150-3000 mesh
Range of application: calcium carbonate, kaolin, carbon black, dolomite…… [Read More…]
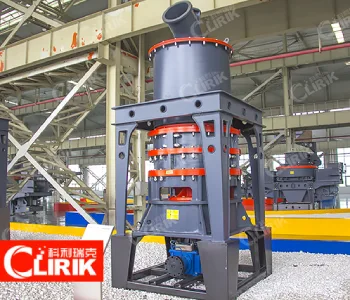
Talc Ultrafine Grinding Mill
Capacity: 0.2-45 t/h
Max feeding size: 20 mm
Discharge fineness: 150-3000 mesh
Processing materials: non-flammable and explosive non-metallic ores with Mohs hardness less than 7…… [Read More…]
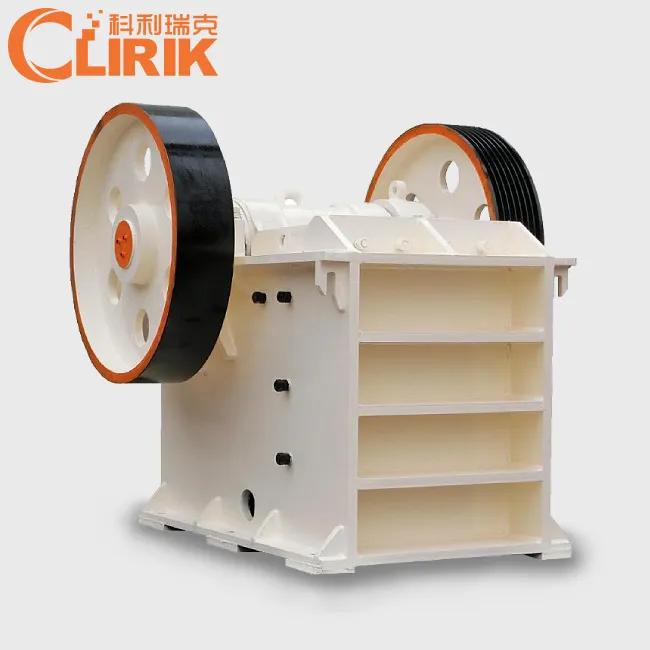
Talc Jaw Crusher
Output Size: 65-160mm
Feed size: 480mm
Capacity: 1-140t/h
Processing materials: Granite, quartz stone, river pebble, calcite, concrete, dolomite…… [Read More…]
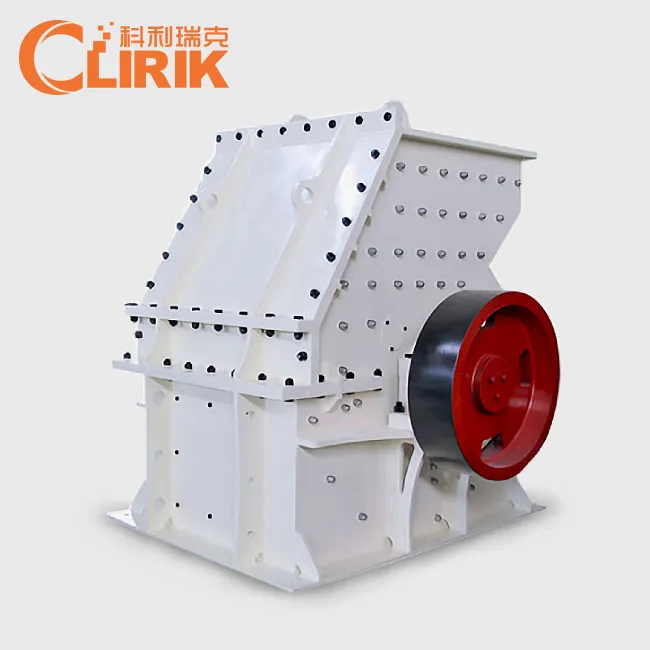
Talc Hammer Mill
Output Size: 5-20 mm
Feed size: <350 mm
Capacity: 5-30 t/h
Application: It is widely used for medium and fine crushing of brittle, medium hardness and soft materials... [Read More…]
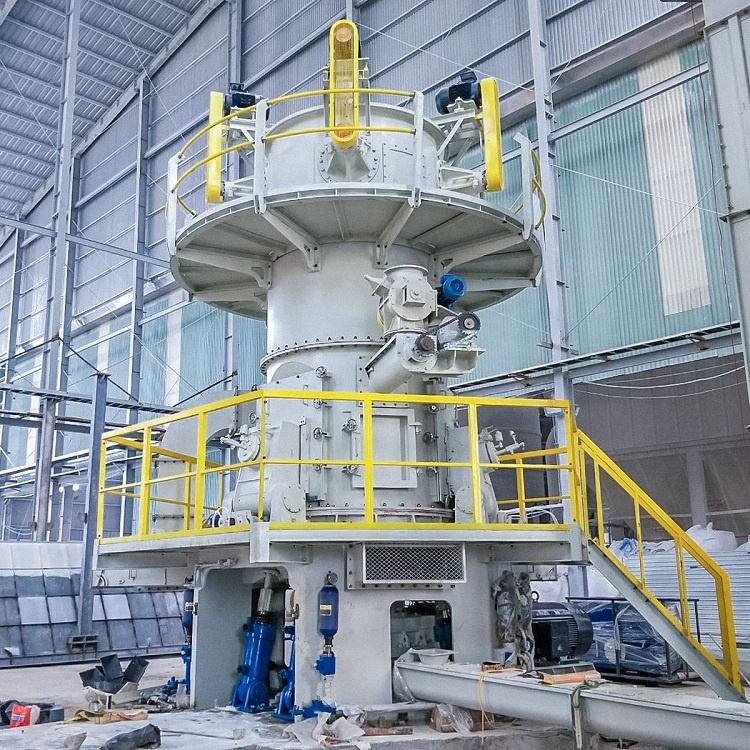
Talc Vertical Mill
Discharge fineness: 150-3000 mesh
Feed size: <15 mm
Output: 1-20 T/H
Product features: It has high grinding efficiency, low energy consumption, uniform particle shape... [Read More…]