The general coating consists of film-forming substances, solvents, pigments, additives, and fillers. Filler is the largest component of paint except film-forming substances, so the choice of filler is critical to the performance of the paint.
The role of fillers in paint is mainly in the following aspects:
Improve the mechanical strength of paints and coatings;
Filling effect, increase the solid content, reduce the amount of resin and solvent, and reduce costs; Give the paint good fluidity, construction performance, increase the thickness of the coating film; Provide partial covering, weather resistance, UV resistance, extend the service life of the coating film; Special functionality, such as ultraviolet shielding, heat resistance, and minimal toxicity; Improve the performance of other additives, such as thickeners, rheological agents, antistatic agents, ultraviolet light stabilizers, etc.
Fillers mainly include calcium carbonate, barite powder, quartz powder, talc powder, kaolin, mica powder, wollastonite, dolomite, etc. These fillers have different composition structures and chemical properties, but they all have common characteristics. These characteristics are necessary as coating fillers:
White or light color, whiteness requirements are generally above 90%; Small particle size, narrow particle size distribution, easy to disperse, can cover the coating evenly and comprehensively; It must have low oil absorption and low oil absorption value to increase the critical pigment volume concentration of the coating, save resin base material, and meet the requirements of modern high solids coatings. It can make the paint have good rheological properties (fluidity, leveling, suspension, thickening, etc.), so that the paint does not precipitate during storage, which is convenient for film formation during construction and forms a smooth and smooth coating film; Good compatibility with other components of the coating film without chemical reaction with other components; Have appropriate specific surface area, particle shape and crystal morphology. It directly affects the viscosity, dispersion stability, refractive index and other properties of the coating.
1. Calcium carbonate:
Calcium carbonate is the most commonly used filler in coatings. It is also widely used in the plastics industry and paper industry. Calcium carbonate has good weather resistance, high strength, low price (common coating filler is the lowest), wear resistance, can improve the corrosion resistance of the coating and the rheology of the coating, can also reduce the pulverization rate, improve color retention, and improve pollution resistance Performance, shortcomings are easy to frost.
2. Talcum powder:
Talc powder, also called hydrous magnesium silicate, is directly crushed from talc ore. It has good lipophilicity, it is easy to disperse in solvent-based coatings and will not form agglomerate precipitates, it is the main filler of solvent-based coatings, but it is easy to cause agglomerate precipitates in water-based paints, so the amount is less because it is very It has strong oil absorption and is not commonly used in powder coatings. Talc is basically fibrous or flake-shaped, with good weather resistance, but poor fluidity in coatings, and insufficient film flatness; flake-shaped talc powder can improve paint leveling, flatness and gloss retention. Its chemical properties are extremely stable and can withstand high temperatures of 900 degrees. Its disadvantage is that it is easy to powder and should be used in an appropriate amount.
We produce calcium carbonate grinding mill and talcum powder making machine. For people who requires calcium carbonate powder or talcum powder no more than 3000 mesh, we can absolutely reach that needs. More information can be sent to you if you are interested.
HOT PRODUCTS
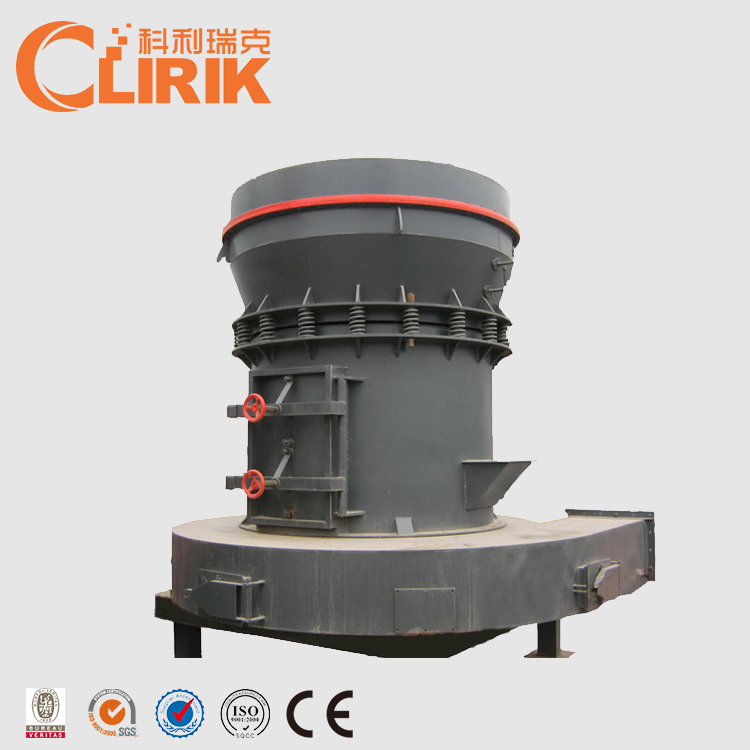
Talc Raymond Mill
Capacity: 1-25 t/h
Max feeding size: 40 mm
Discharge fineness: 50-325 mesh
Range of application: Barite, calcite, potassium feldspar, talc…… [Read More…]
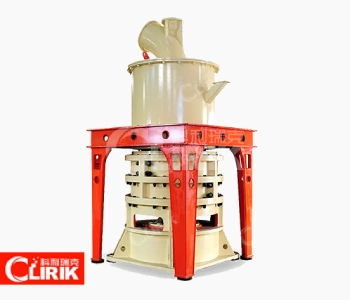
Micro Powder Grinding Mill
Capacity: 0.2-45 t/h
Max feeding size: 20 mm
Discharge fineness: 150-3000 mesh
Range of application: calcium carbonate, kaolin, carbon black, dolomite…… [Read More…]
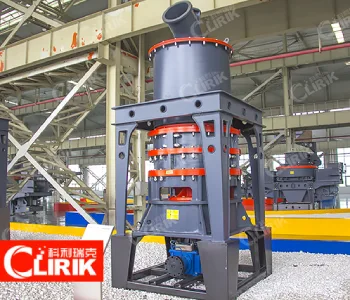
Talc Ultrafine Grinding Mill
Capacity: 0.2-45 t/h
Max feeding size: 20 mm
Discharge fineness: 150-3000 mesh
Processing materials: non-flammable and explosive non-metallic ores with Mohs hardness less than 7…… [Read More…]
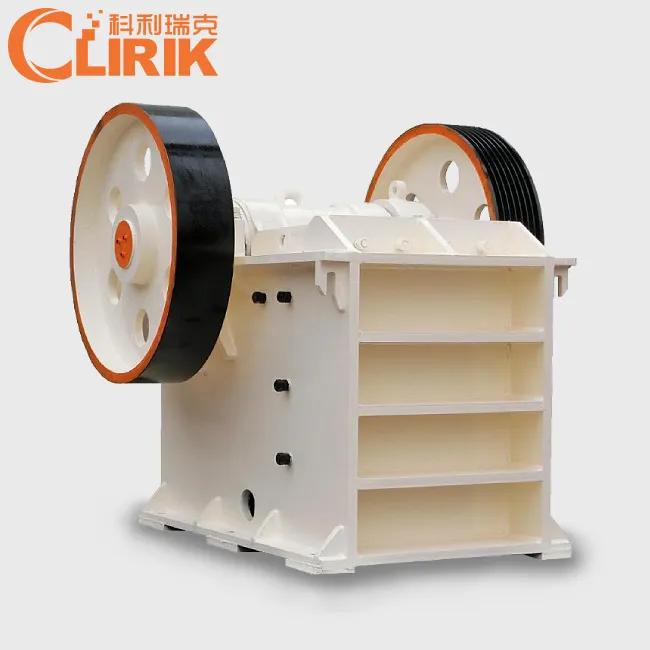
Talc Jaw Crusher
Output Size: 65-160mm
Feed size: 480mm
Capacity: 1-140t/h
Processing materials: Granite, quartz stone, river pebble, calcite, concrete, dolomite…… [Read More…]
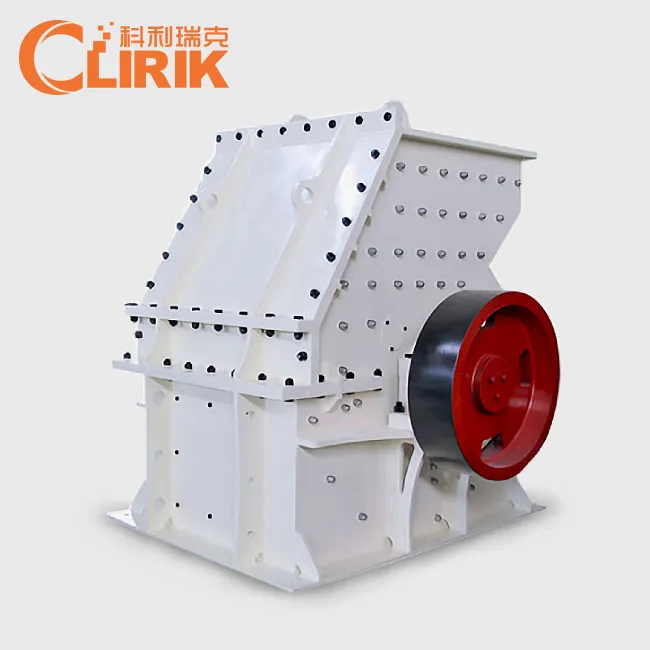
Talc Hammer Mill
Output Size: 5-20 mm
Feed size: <350 mm
Capacity: 5-30 t/h
Application: It is widely used for medium and fine crushing of brittle, medium hardness and soft materials... [Read More…]
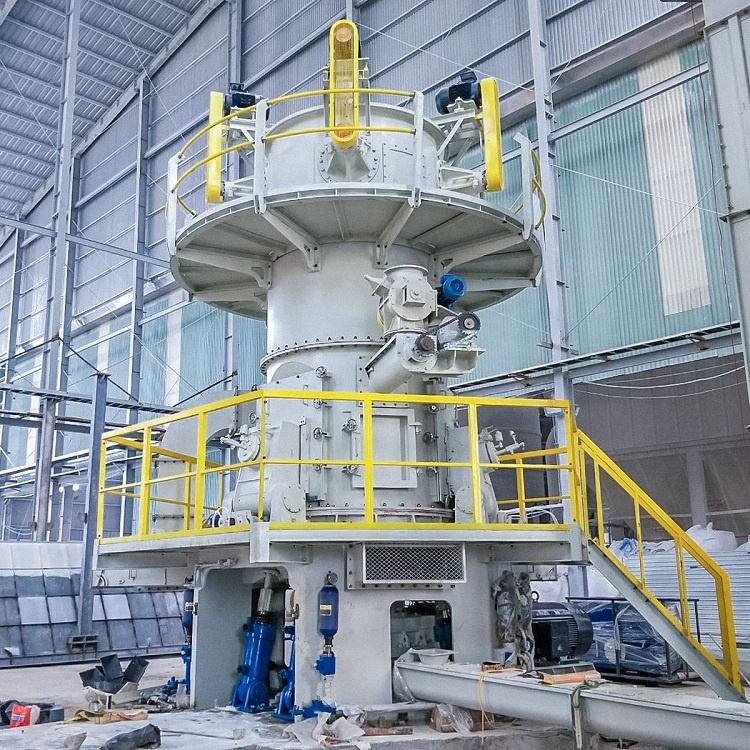
Talc Vertical Mill
Discharge fineness: 150-3000 mesh
Feed size: <15 mm
Output: 1-20 T/H
Product features: It has high grinding efficiency, low energy consumption, uniform particle shape... [Read More…]