- What is phase separation of dry mixture?
Phase separation refers to the unstable tendency of objects to separate due to changes in certain environmental conditions. The dry mix is composed of PVC particles that absorb inorganic substances and additives. Due to the low viscosity of PVC, the various components of the inorganic substance contained in it peel off from the PVC particles, resulting in uneven dispersion, which is the phase separation of the dry mixture. This phenomenon can cause pitting, pinholes and micro-interface defects inside the product on the external appearance of the produced product, which will reduce the material performance.
2.Influencing factors of phase separation of dry mixture
The main factors are the production of auxiliary materials, mixing process and transmission method.
- Production accessories
The main auxiliary materials used in the processing of PVC are stabilizers, titanium dioxide, CPE, CaCo3, ACR and pigments. Generally speaking, CaCo3 is the inorganic substance with the largest amount in the entire formulation system.
The activation degree of CaCo3 is an important index to measure its affinity with organic matrix. Increasing the activation degree of CaCo3 can greatly reduce the degree of phase separation. At present, the main activators used for CaCo3 activation are stearic acid and coupling agents. Stearic acid is activated by physically wrapping calcium carbonate, and coupling agent activation is mainly through chemical reaction or molecular chain winding to wrap calcium carbonate. The coupling agent is centered on titanium or aluminum or zirconium. One end of the molecule can react with the chemical group on the surface of the inorganic substance to form a strong chemical bond; the other end group has the nature of an organophile, which can react with organic molecules or physically entangle. , So that two materials with very different properties are firmly combined.
The activation degree of CaCo3 in the production auxiliary material has a great influence on the phase separation of the dry mixture.
- Mixing process
Mixing is actually a process of compaction, homogenization, moisture removal, and pre-gelation after mixing the production accessories and PVC. In the whole process, the micro-components of the auxiliary materials are adsorbed on the surface of the PVC particles. After friction and shearing, the PVC resin is gradually melted and plasticized, and then recrystallized to form a network structure. In the process of high-speed thermal mixing, it can be seen that the PVC resin not only has finer particles and uniform particle size, but also shows the characteristics of increased density and partial gelation, and finally a uniform dry mixture is formed.
Therefore, the setting of the mixing process directly affects the degree of phase separation.
HOT PRODUCTS
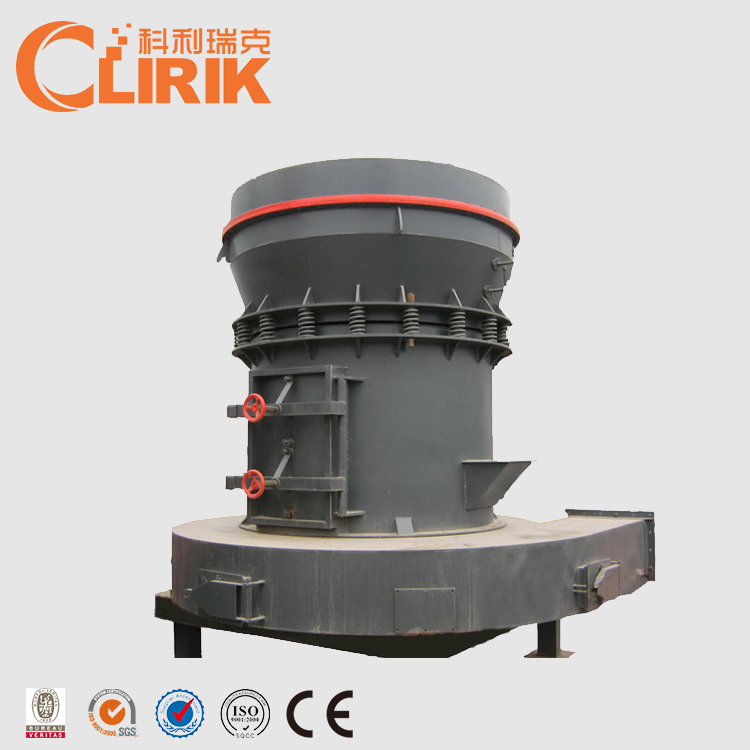
Talc Raymond Mill
Capacity: 1-25 t/h
Max feeding size: 40 mm
Discharge fineness: 50-325 mesh
Range of application: Barite, calcite, potassium feldspar, talc…… [Read More…]
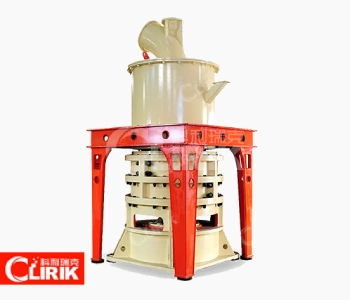
Micro Powder Grinding Mill
Capacity: 0.2-45 t/h
Max feeding size: 20 mm
Discharge fineness: 150-3000 mesh
Range of application: calcium carbonate, kaolin, carbon black, dolomite…… [Read More…]
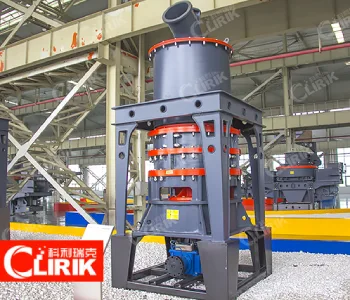
Talc Ultrafine Grinding Mill
Capacity: 0.2-45 t/h
Max feeding size: 20 mm
Discharge fineness: 150-3000 mesh
Processing materials: non-flammable and explosive non-metallic ores with Mohs hardness less than 7…… [Read More…]
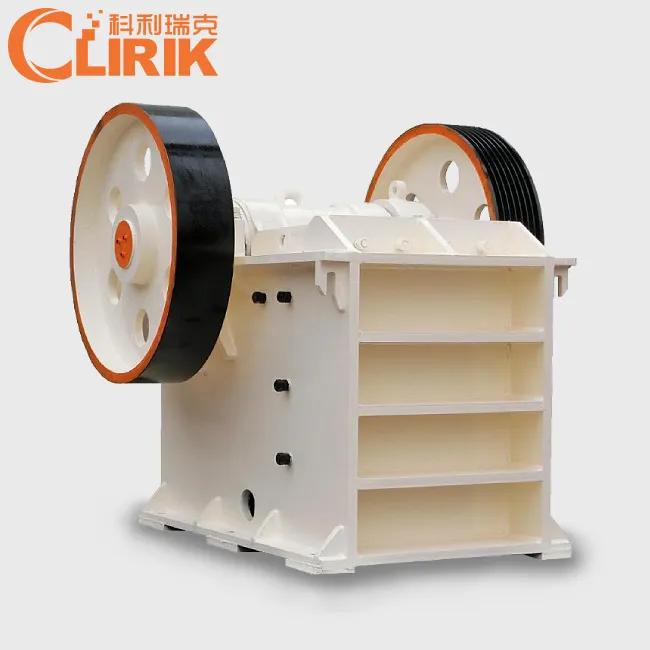
Talc Jaw Crusher
Output Size: 65-160mm
Feed size: 480mm
Capacity: 1-140t/h
Processing materials: Granite, quartz stone, river pebble, calcite, concrete, dolomite…… [Read More…]
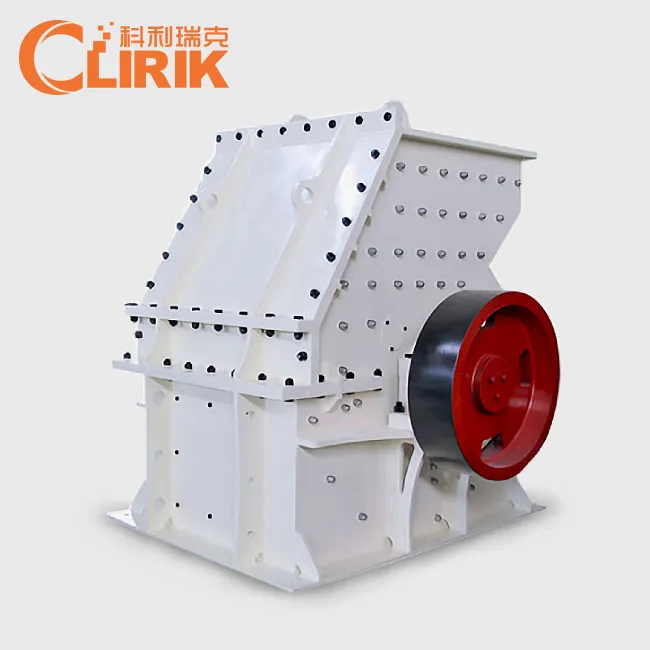
Talc Hammer Mill
Output Size: 5-20 mm
Feed size: <350 mm
Capacity: 5-30 t/h
Application: It is widely used for medium and fine crushing of brittle, medium hardness and soft materials... [Read More…]
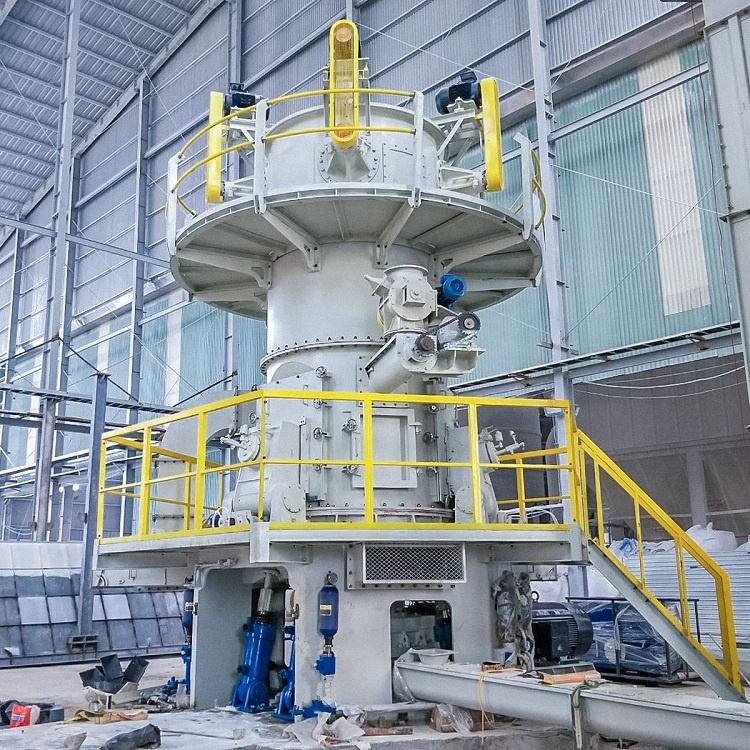
Talc Vertical Mill
Discharge fineness: 150-3000 mesh
Feed size: <15 mm
Output: 1-20 T/H
Product features: It has high grinding efficiency, low energy consumption, uniform particle shape... [Read More…]