Powder surface modification refers to the use of physical, chemical, mechanical and other methods to treat the surface of the powder. According to the needs of the application, the physical and chemical properties of the powder surface are changed purposely or given new functions to meet the needs of modern new materials, The need for the development of new processes and new technologies.
Reason 1: Enhance dispersion
In the polymer material industry such as plastics, rubber, adhesives, and polymer-based composite materials, inorganic mineral fillers occupies a very important position. However, due to the different surface or interface properties of the inorganic powder filler and the matrix, that is, the organic polymer, the compatibility is poor, so it is difficult to uniformly disperse in the matrix. Direct or excessive filling tends to lead to certain mechanical properties of the material. Defects and easy embrittlement. Therefore, the surface of the inorganic powder filler must be modified to improve the physical and chemical properties of its surface, enhance its compatibility with the matrix, that is, the organic polymer or resin, and its dispersibility in the organic matrix, so as to improve The mechanical strength and comprehensive performance of the material.
Surface modification is one of the necessary processing methods for inorganic fillers to change from general incremental fillers to functional fillers. It also provides new technical methods for the development of polymer materials and organic/inorganic composite materials. This is the powder surface One of the main purposes of modification.
Reason 2: Improve the dispersion of pigments and fillers and improve coating performance
Improving the dispersion of pigments in paints or paints, and improving the gloss, tinting power, hiding power, weather resistance, heat resistance, antibacterial and mildew resistance, and color retention of the coating are the second main purpose of powder surface modification. .
The coloring pigments and extender pigments of coatings are mostly inorganic powders. In order to improve their dispersibility in organic-based paints or coatings, they must be surface modified to improve the wettability of the surface and enhance the bonding force with the matrix.
The fillers and pigments in the newly developed so-called special coatings that have the functions of electricity, magnetism, sound, heat, light, antibacterial, mildew, anticorrosion, radiation protection, special decoration, etc. not only require ultra-fine particle size, but also require certain functions.” . Therefore, it must be surface treated.
In addition, in order to improve the weather resistance, heat resistance, hiding power and tinting power of certain pigments, coating with some better performance inorganic substances, such as coating titanium dioxide with alumina and silica can improve its weather resistance And other performance.
Reason 3: Give pigments and fillers good dispersion stability and rheology
In addition to compatibility and compatibility with other components, inorganic pigments and fillers are also required to have long-term dispersion stability and good rheological properties in water-based architectural decorative coatings that have become one of the current popular trends. This is one of the reasons why the pigments and fillers used in water-based coatings must be surface modified or treated.
Reason 4: Give the product a pearlescent effect
Many high value-added products today require good optical and visual effects to make the products more colorful. This requires surface treatment of some powder raw materials to give the products good gloss and decorative effects. For example, muscovite powder is surface-modified by metal oxides such as titanium oxide, chromium oxide, iron oxide, zirconium oxide, etc., and used in cosmetics, plastic products, light-colored rubber, paint, special coatings, leather, etc., which can give these products a pearlescent effect. , Which significantly increases the value of these products.
Reason 5: Improve the dispersibility of inorganic pigments
In the new inorganic/inorganic composite material, the dispersibility between the inorganic components has a great influence on the final performance of the material. Especially when small-component ceramic pigments are dispersed in large-component ceramic blanks, such as ceramic pigments added to colored ceramic floor tiles, their dispersibility directly affects the uniformity of the color of the ceramic product and the grade of the product. The use of ceramic pigments with good dispersibility can not only make the color of the final product good, but also reduce the amount of expensive pigments. Therefore, the surface treatment of inorganic pigments or components (improving the dispersibility in the inorganic phase) is also of great significance to the development of inorganic/inorganic composite materials.
Reason 6: Give functional characteristics and expand application areas
In many powder materials with layered crystal structure, the intercalation modification using the weak molecular bond between the crystal layers or the exchangeability of interlayer ions can produce a new type of mineral interlayer compound. Such as clay intercalation compounds and graphite intercalation compounds. These interlayer compounds have new physical and chemical properties or functions that the original mineral powder does not have.
For example, the interlayer compound made by the interlayer chemical treatment of graphite has much better properties than graphite. It has excellent properties or functions such as high temperature resistance, thermal shock resistance, anti-oxidation, corrosion resistance, lubricity and sealing. It is a new type of conductive Raw materials for materials, electrode materials, hydrogen storage materials, flexible graphite, and sealing materials, and their applications have been expanded to metallurgy, petroleum, chemical, machinery, aerospace, atomic energy, new energy and other fields.
The organic modified bentonite between layers of organic bentonite also shows good swelling, adsorption, thixotropy and bonding properties in non-polar and weakly polar solvents.
Reason 7: Improve powder adsorption, catalysis and other characteristics
For adsorption and catalytic powder materials, in order to improve their adsorption and catalytic activity, selectivity, stability, mechanical strength and other properties, surface treatment or surface modification is also required.
For example, on the surface of activated carbon, diatomaceous earth, alumina, silica gel, sepiolite, zeolite and other powders, metal oxides, alkali or alkaline earth metals, rare earth oxides, copper, silver, gold, aluminum, diamond, Platinum, bar, nickel and other metals or precious metals.
Reason 8: Let nano powders become real “nano powders”
Nano powder is a new powder material developed on the basis of micron powder, which has good application prospects. However, the nano powder has a large specific surface area, a large number of surface atoms, and a high surface energy. It is easy to agglomerate to form secondary, tertiary or larger particles during preparation, storage, transportation and use, so that it cannot exert its due nano effect. . Therefore, the surface treatment or surface modification of nano-powders is of vital importance for improving and enhancing the application performance of nano-powders and accelerating its industrial application.
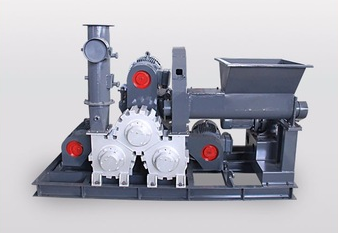
CLIRIK CLG series powder modifiers, are continuous operation, large capacity, suitable for industrialization production in various scale. Both modifying and dispersion function, suitable for any fine materials. Running at vacuum, airtight, no dust leakage, no pollution, good operation condition, low labor intensity etc.,
If you are interested in our product, welcom to contact us for inquiry now!
HOT PRODUCTS
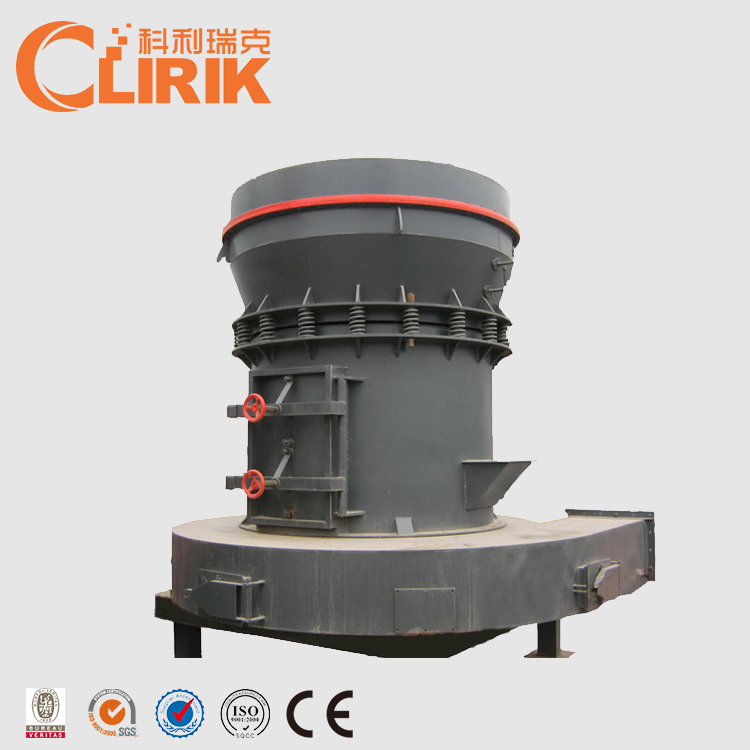
Talc Raymond Mill
Capacity: 1-25 t/h
Max feeding size: 40 mm
Discharge fineness: 50-325 mesh
Range of application: Barite, calcite, potassium feldspar, talc…… [Read More…]
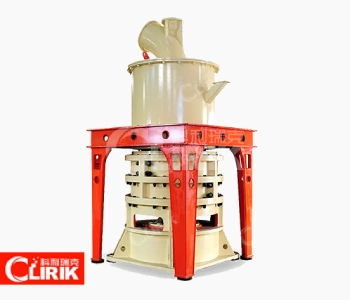
Micro Powder Grinding Mill
Capacity: 0.2-45 t/h
Max feeding size: 20 mm
Discharge fineness: 150-3000 mesh
Range of application: calcium carbonate, kaolin, carbon black, dolomite…… [Read More…]
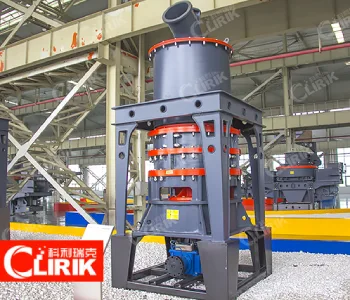
Talc Ultrafine Grinding Mill
Capacity: 0.2-45 t/h
Max feeding size: 20 mm
Discharge fineness: 150-3000 mesh
Processing materials: non-flammable and explosive non-metallic ores with Mohs hardness less than 7…… [Read More…]
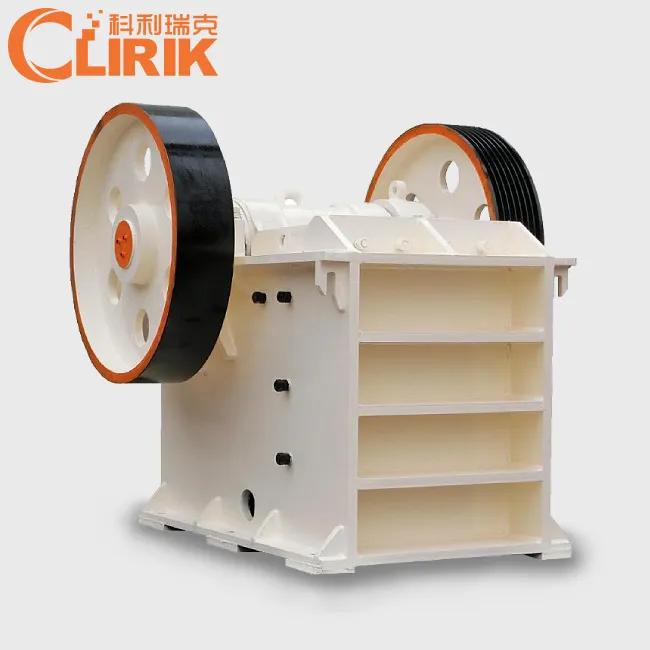
Talc Jaw Crusher
Output Size: 65-160mm
Feed size: 480mm
Capacity: 1-140t/h
Processing materials: Granite, quartz stone, river pebble, calcite, concrete, dolomite…… [Read More…]
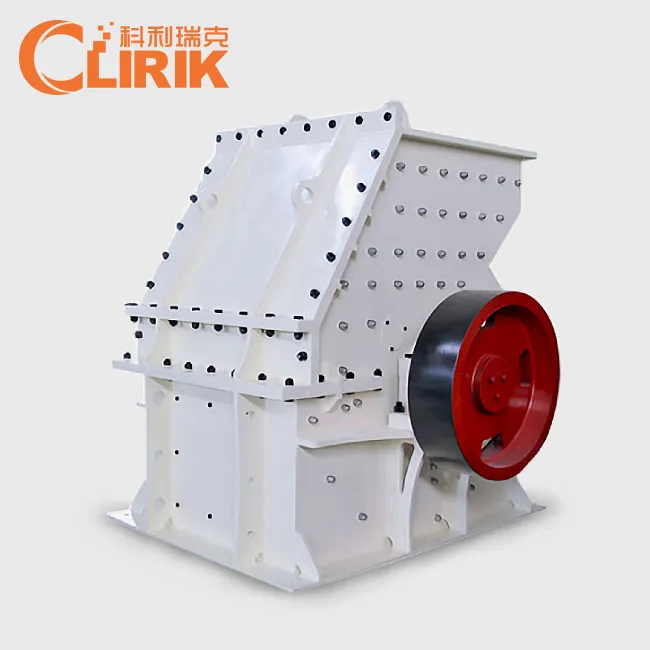
Talc Hammer Mill
Output Size: 5-20 mm
Feed size: <350 mm
Capacity: 5-30 t/h
Application: It is widely used for medium and fine crushing of brittle, medium hardness and soft materials... [Read More…]
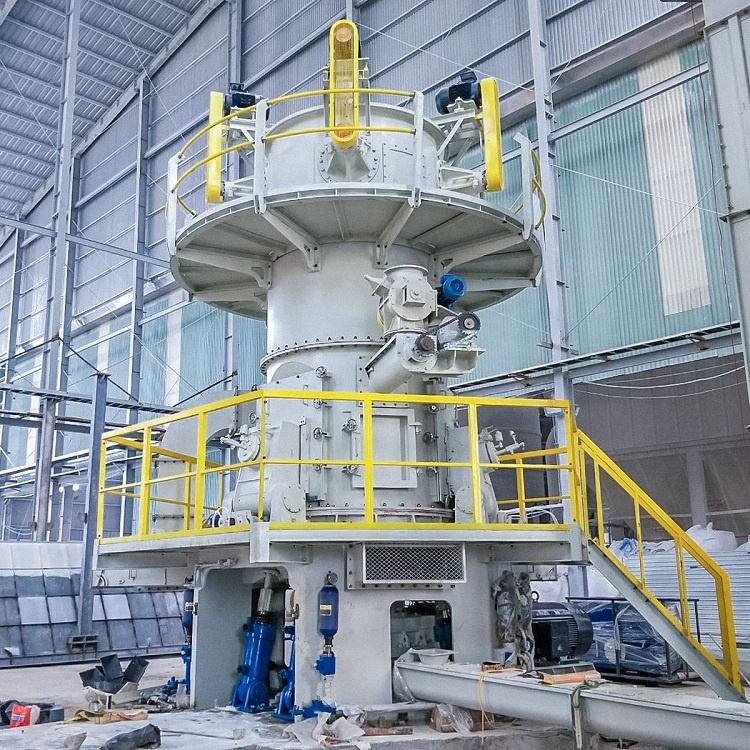
Talc Vertical Mill
Discharge fineness: 150-3000 mesh
Feed size: <15 mm
Output: 1-20 T/H
Product features: It has high grinding efficiency, low energy consumption, uniform particle shape... [Read More…]