The talc vertical mill is a device that continuously collides with the material through the grinding roller, and generates a certain squeezing force for the stone that enters the grinding zone evenly, so as to crush it. The output is first selected the model and quantity of the mill, and then distributed to each process system. Reasonably choose the model and quantity of the mill to make the vertical milling process reasonable and perfect. We often hear the saying “the larger the design output, the more perfect the process”. The fundamental reason is that the more pulverizers and the finer the distribution of the system, the greater the flexibility of system adjustment and the more complete the process. As a result, the quality of the finished powder and the efficiency of the equipment will be greatly improved.
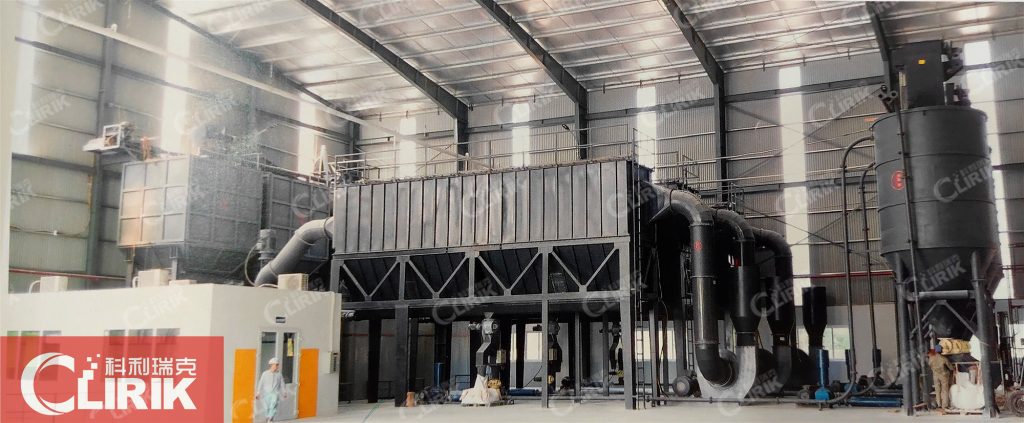
When it overflows the grinding disc and encounters the high-speed airflow passing through the wind ring, the finer materials are blown up by the airflow, while the coarse materials that cannot be blown by the airflow fall into the annular air duct and are scraped out of the grinding body by the scraping device and fed. Enter the circulating elevator and return to the mill for squeezing and crushing. At this time, the material that is blown up by the airflow, due to the decrease of airflow velocity during the ascent process, the coarser material will fall back to the grinding plate and be crushed again, and the material that continues to be carried by the airflow will follow the airflow to the static state. In the powder selection area of the combined powder separator, the coarse and fine powder are separated under the action of the rotating cage rotor. The coarse powder falls off the grinding plate and is squeezed and crushed again. The fine powder flows to the cyclone to separate the fine powder and gas.
The reasonable use of talc vertical mill equipment can save investment and reduce operating costs. While meeting the powder requirements, different types of mills can be matched to reduce investment. However, there are always gains and losses in any measure. Although the use of different types of mills can reduce investment and operating costs, it also inevitably brings about the problem of increasing the purchase of mill parts and affecting the aesthetics of the workshop layout. Must be based on the design output, based on the rationality and advancement of the process, based on the comparison and analysis of different configuration plans, and then finally specify a set of reasonable price plans for customers to choose according to customer needs.
HOT PRODUCTS
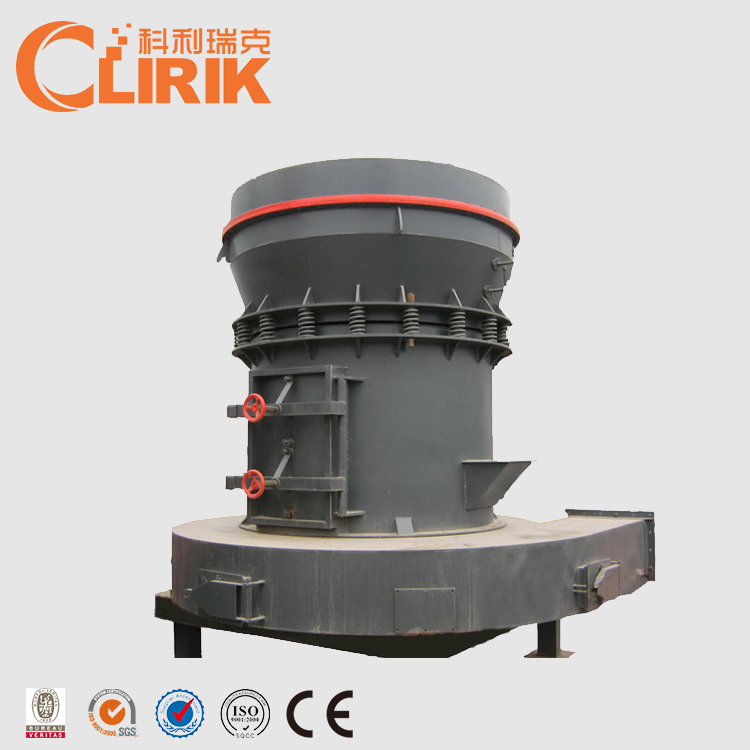
Talc Raymond Mill
Capacity: 1-25 t/h
Max feeding size: 40 mm
Discharge fineness: 50-325 mesh
Range of application: Barite, calcite, potassium feldspar, talc…… [Read More…]
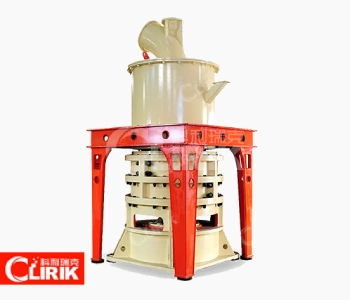
Micro Powder Grinding Mill
Capacity: 0.2-45 t/h
Max feeding size: 20 mm
Discharge fineness: 150-3000 mesh
Range of application: calcium carbonate, kaolin, carbon black, dolomite…… [Read More…]
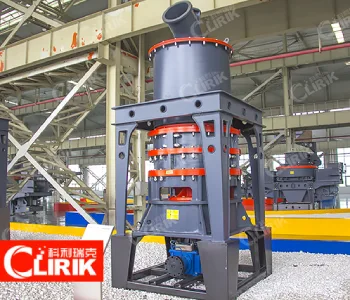
Talc Ultrafine Grinding Mill
Capacity: 0.2-45 t/h
Max feeding size: 20 mm
Discharge fineness: 150-3000 mesh
Processing materials: non-flammable and explosive non-metallic ores with Mohs hardness less than 7…… [Read More…]
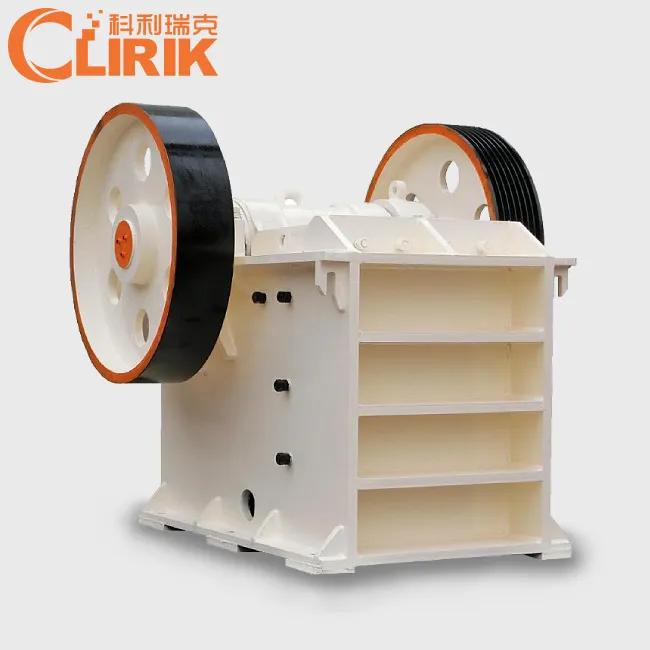
Talc Jaw Crusher
Output Size: 65-160mm
Feed size: 480mm
Capacity: 1-140t/h
Processing materials: Granite, quartz stone, river pebble, calcite, concrete, dolomite…… [Read More…]
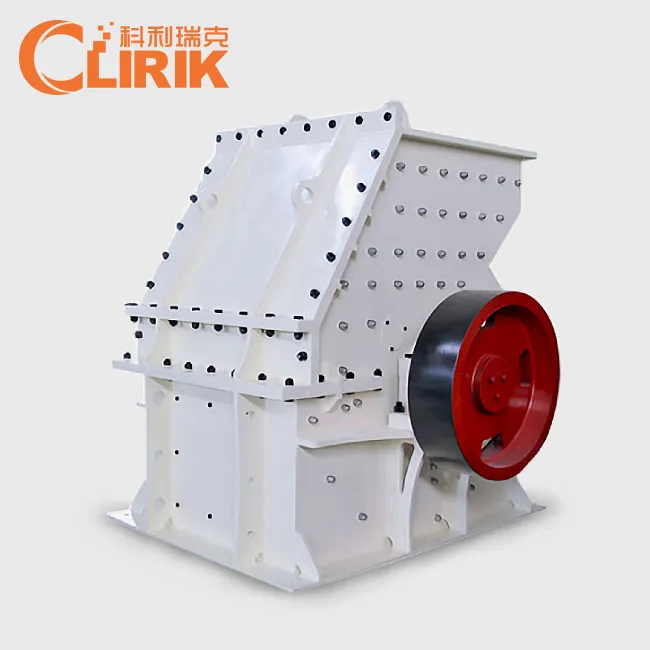
Talc Hammer Mill
Output Size: 5-20 mm
Feed size: <350 mm
Capacity: 5-30 t/h
Application: It is widely used for medium and fine crushing of brittle, medium hardness and soft materials... [Read More…]
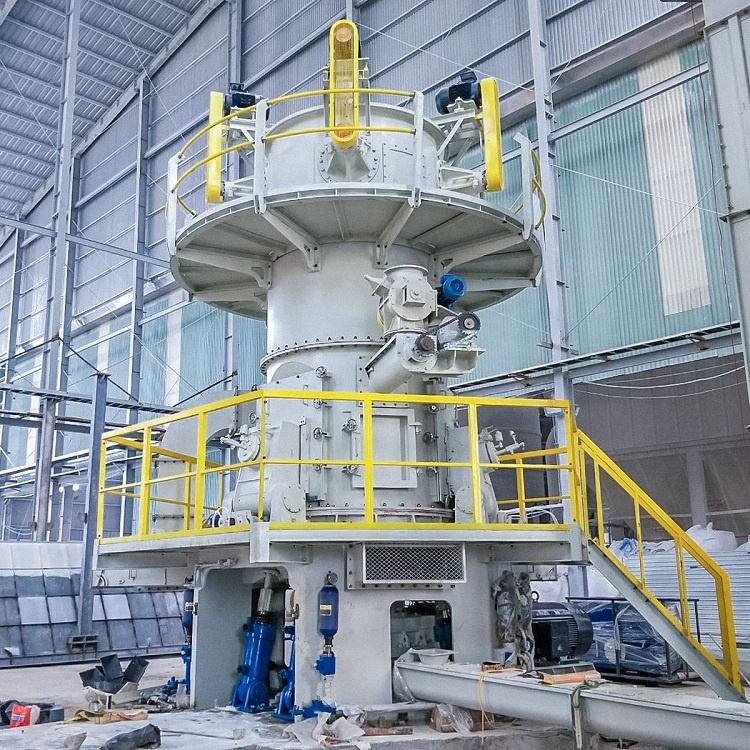
Talc Vertical Mill
Discharge fineness: 150-3000 mesh
Feed size: <15 mm
Output: 1-20 T/H
Product features: It has high grinding efficiency, low energy consumption, uniform particle shape... [Read More…]