Calcium carbonate filled masterbatch is a granule made of calcium carbonate mixed with carrier resin, mixed and granulated, which is similar to the base resin volume of plastic products, and has wide application value in the plastics industry. Before processing the masterbatch, the surface modification of the calcium carbonate powder is performed to increase its dispersibility, which can greatly improve the crosslinkability with the resin.
Here, we share two issues that need to be paid attention to in the production process of calcium carbonate filled masterbatch:
1. Surface modification treatment of calcium carbonate
To make the calcium carbonate particles in the filler masterbatch evenly dispersed into the matrix plastic, the calcium carbonate particles must be completely coated. If the calcium carbonate has been agglomerated during the production of the masterbatch, then in the blown film extruder, such agglomerated particles cannot be opened, and many white spots are bound to form on the film. Even white hard particles may form “clouds”.
To solve the problem of agglomeration of calcium carbonate particles, we should pay attention to two aspects:
The first is to prevent excessive friction during surface treatment. Once static electricity is generated due to friction, reunion is likely to occur.
Secondly, the amount of surface treatment agent should be sufficient. When the particle surface is changed to lipophilic by the action of the coupling agent, its surface energy is greatly reduced, and it is not easy to agglomerate with each other.
2. Filling ratio of calcium carbonate
The higher the proportion of calcium carbonate in the filler masterbatch, the lower the raw material cost of the product and the more competitive the market. Because the particle size of calcium carbonate particles is small, the number of particles is large, and the total surface area is also large, more carrier resin is required to coat it. Not only is the melt viscosity of the carrier resin required to be small, but also a sufficient amount.
In order to obtain a film-grade filling masterbatch with good performance, the weight percentage of calcium carbonate is generally not more than 80%, and the weight percentage of carrier resin is generally not less than 13%.
We produces calcium carbonate powder modificaiton machine( calcium carbonate powder coating machine). If there is any needs, please contact us.
HOT PRODUCTS
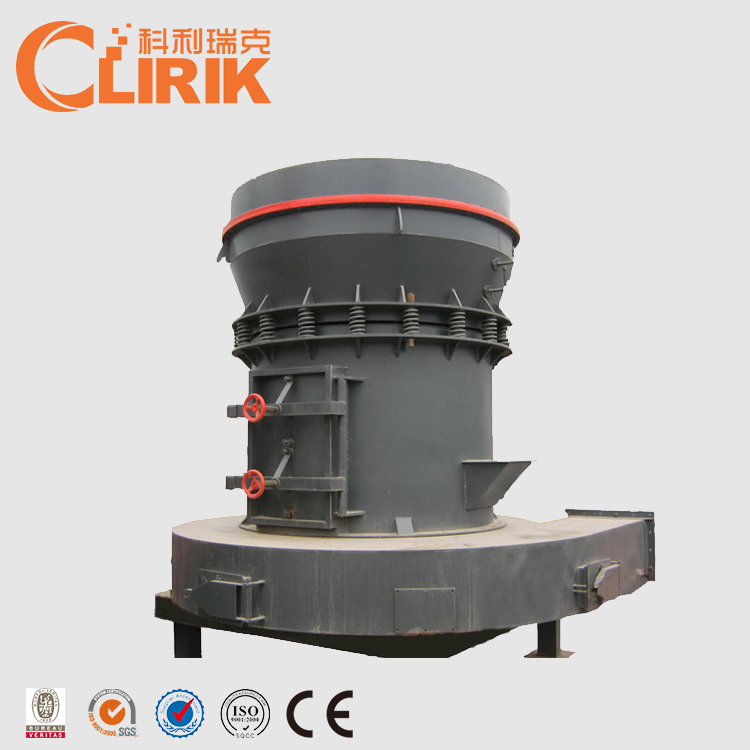
Talc Raymond Mill
Capacity: 1-25 t/h
Max feeding size: 40 mm
Discharge fineness: 50-325 mesh
Range of application: Barite, calcite, potassium feldspar, talc…… [Read More…]
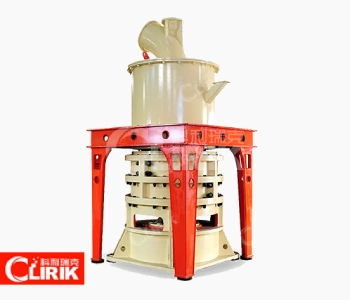
Micro Powder Grinding Mill
Capacity: 0.2-45 t/h
Max feeding size: 20 mm
Discharge fineness: 150-3000 mesh
Range of application: calcium carbonate, kaolin, carbon black, dolomite…… [Read More…]
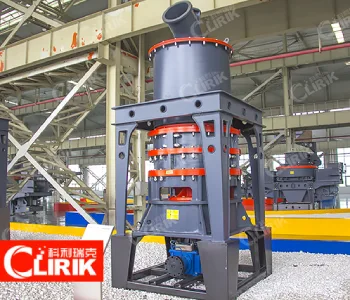
Talc Ultrafine Grinding Mill
Capacity: 0.2-45 t/h
Max feeding size: 20 mm
Discharge fineness: 150-3000 mesh
Processing materials: non-flammable and explosive non-metallic ores with Mohs hardness less than 7…… [Read More…]
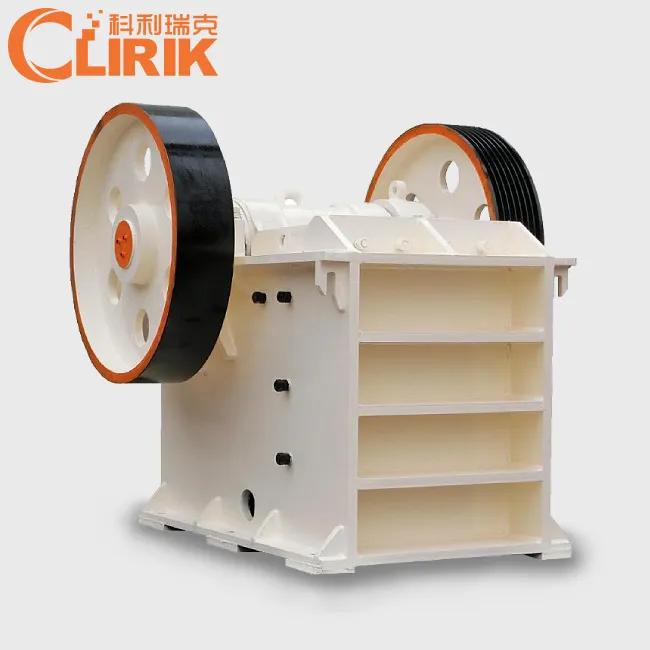
Talc Jaw Crusher
Output Size: 65-160mm
Feed size: 480mm
Capacity: 1-140t/h
Processing materials: Granite, quartz stone, river pebble, calcite, concrete, dolomite…… [Read More…]
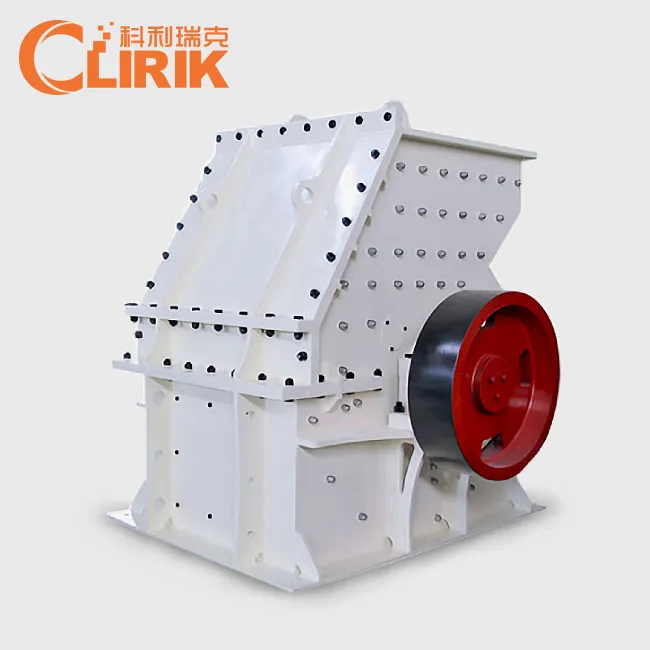
Talc Hammer Mill
Output Size: 5-20 mm
Feed size: <350 mm
Capacity: 5-30 t/h
Application: It is widely used for medium and fine crushing of brittle, medium hardness and soft materials... [Read More…]
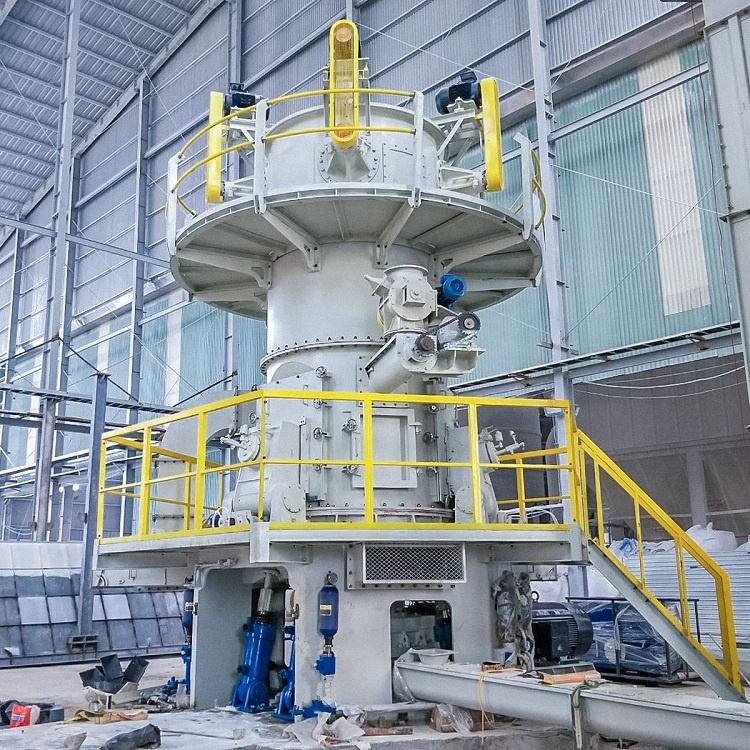
Talc Vertical Mill
Discharge fineness: 150-3000 mesh
Feed size: <15 mm
Output: 1-20 T/H
Product features: It has high grinding efficiency, low energy consumption, uniform particle shape... [Read More…]