Used as a nucleating agent
Crystalline polymers such as polyethylene (PE), polypropylene (PP), polyethylene terephthalate (PET), polyamide (PA), etc., in the process of cooling and setting after processing and melting, some macromolecules The arrangement is orderly and is called crystallization. Crystallization not only requires a certain temperature and cooling rate, but also needs to generate crystal nuclei first, followed by crystal growth. The nucleating agent has two main functions. One is that the total crystallization rate is increased, which can ensure that the molten polymer solidifies more quickly during the cooling process, thereby shortening the injection molding cycle and improving work efficiency. The tensile strength, heat distortion temperature and hardness are enhanced by the nucleating agent, the transparency increases and the turbidity decreases.
The use of talc as a nucleating agent for PE or PP requires the particles to be smaller. The smaller the particle size, the greater the number of particles, which means more crystalline centers. The more the number of crystals grown at the same time, the smaller the size of the crystal itself, the better the performance of the entire material. At the same time, it is also required that the dispersion of the talcum powder in the molten state is as complete as possible, and the agglomeration phenomenon is as slight as possible.
Transparent filler masterbatch with talc as main filler
Although the use of calcium carbonate in plastic films can reduce the cost, when the amount is large, the transparency of the film is greatly affected, causing misunderstanding by some users. In view of this situation, the transparent filler masterbatch with talc as the main filler has made significant improvements in the selection of fillers and processing technology, which has greatly improved the transparency of the PE film.
Talcum powder making machine
Clirik’s mills for talc and other materials can accept non-flammable and explosive materials with a Mohs hardness below 20mm and a Mohs hardness below 6. The crushed raw materials are mainly crushed calcite, gypsum, talc, feldspar, barite, kaolin and other materials. Due to the major changes in the main machine’s grinding roller and grinding roller assembly, the material has to go through many times from top to bottom Grinding makes full use of the role of the centrifugal force of the grinding roller, and the contact area with the grinding ring is large, so it can produce high-fineness powder with a fineness between 5-45 microns.
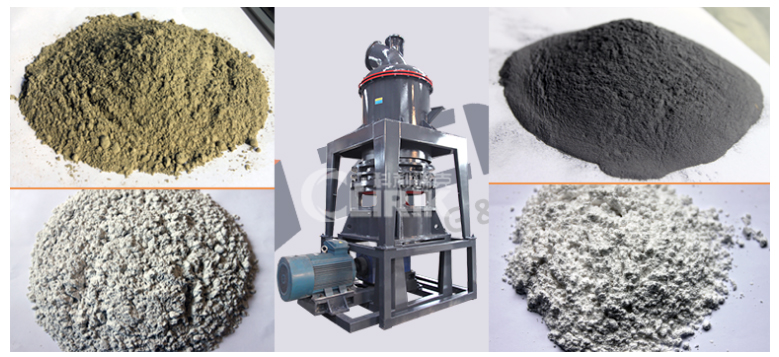
If you are intersted in this HGM talcum powder making machine, please contact us and explain your requirements in details.
HOT PRODUCTS
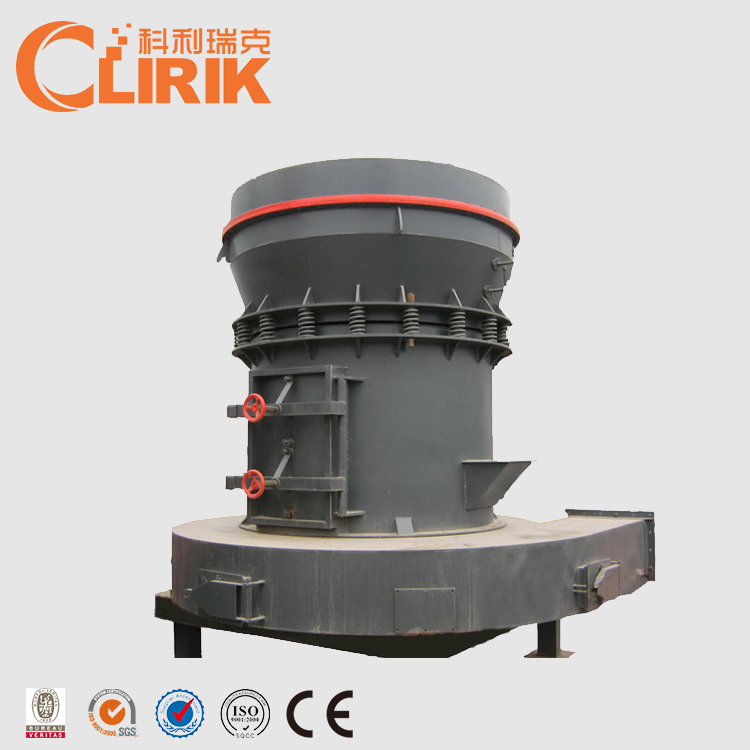
Talc Raymond Mill
Capacity: 1-25 t/h
Max feeding size: 40 mm
Discharge fineness: 50-325 mesh
Range of application: Barite, calcite, potassium feldspar, talc…… [Read More…]
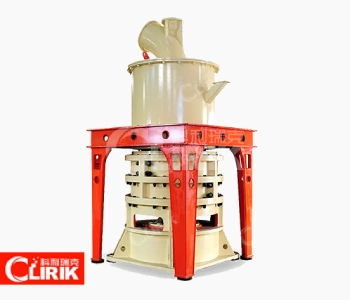
Micro Powder Grinding Mill
Capacity: 0.2-45 t/h
Max feeding size: 20 mm
Discharge fineness: 150-3000 mesh
Range of application: calcium carbonate, kaolin, carbon black, dolomite…… [Read More…]
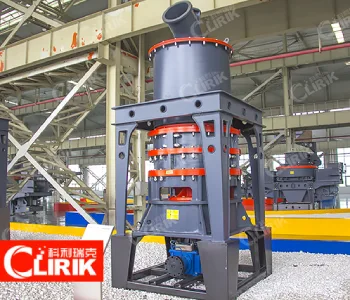
Talc Ultrafine Grinding Mill
Capacity: 0.2-45 t/h
Max feeding size: 20 mm
Discharge fineness: 150-3000 mesh
Processing materials: non-flammable and explosive non-metallic ores with Mohs hardness less than 7…… [Read More…]
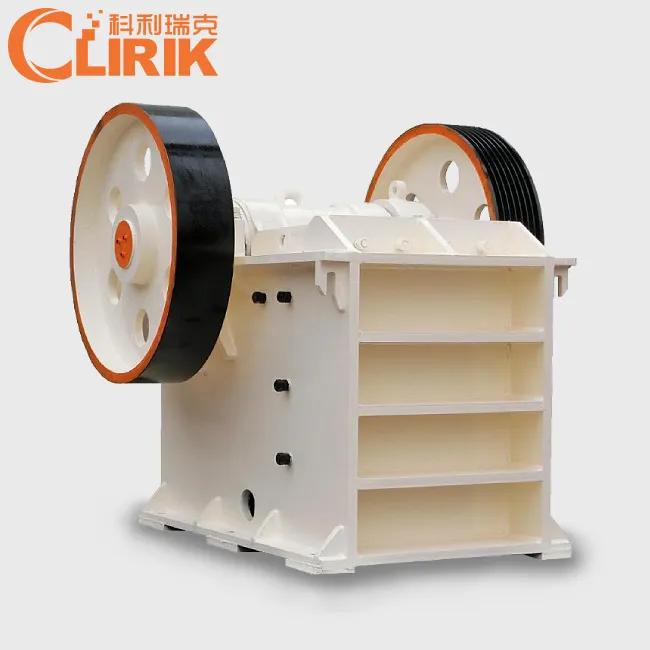
Talc Jaw Crusher
Output Size: 65-160mm
Feed size: 480mm
Capacity: 1-140t/h
Processing materials: Granite, quartz stone, river pebble, calcite, concrete, dolomite…… [Read More…]
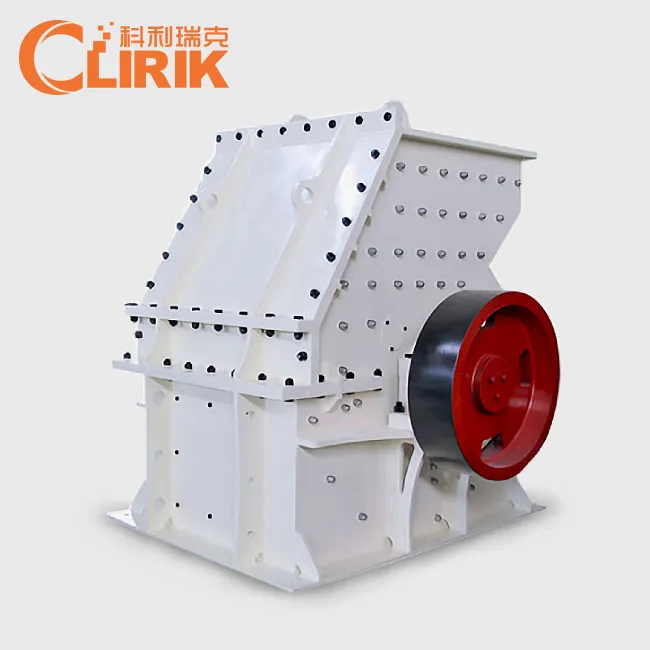
Talc Hammer Mill
Output Size: 5-20 mm
Feed size: <350 mm
Capacity: 5-30 t/h
Application: It is widely used for medium and fine crushing of brittle, medium hardness and soft materials... [Read More…]
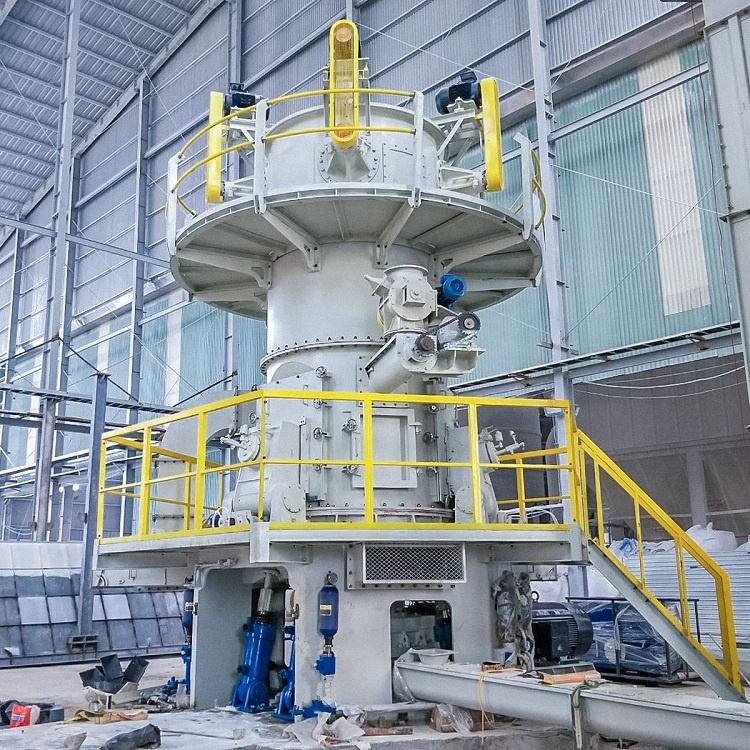
Talc Vertical Mill
Discharge fineness: 150-3000 mesh
Feed size: <15 mm
Output: 1-20 T/H
Product features: It has high grinding efficiency, low energy consumption, uniform particle shape... [Read More…]