The 1000 mesh fine powder mill is suitable for the preparation of various ore powders and coal powders, such as fine powder processing of raw materials, gypsum ore, coal and other materials. The working principle of micro-powder grinding is that the grinding roller is tightly rolled on the grinding ring under the action of centrifugal force, and the material is shoveled by the blade to the middle of the grinding roller and the grinding ring. The material is broken into powder under the action of the rolling pressure, and then Under the action of the fan, the powdered material is blown up and passed through the analysis machine. The material that meets the fineness requirements passes through the analysis machine, and cannot be returned to the grinding chamber to continue grinding. The material is separated and collected by the cyclone separator in the analysis machine.
The talc ultra fine powder grinding machine has a three-dimensional structure, has a small footprint, and has a strong complete set. It independently forms a production system from block materials to finished powder. The fineness of the finished powder is uniform, and the pass rate is 99%, which is difficult for other milling equipment. The transmission device of the main unit of the mill adopts a closed gear box and a belt wheel, and the transmission is stable and the operation is reliable. The important parts of talc ultra fine powder grinding machine are made of high-quality steel, and the wear parts are made of high-performance wear-resistant materials. The whole machine has high wear resistance and reliable operation. The electrical system adopts centralized control, the milling workshop can basically realize unmanned operation, and the maintenance is convenient.
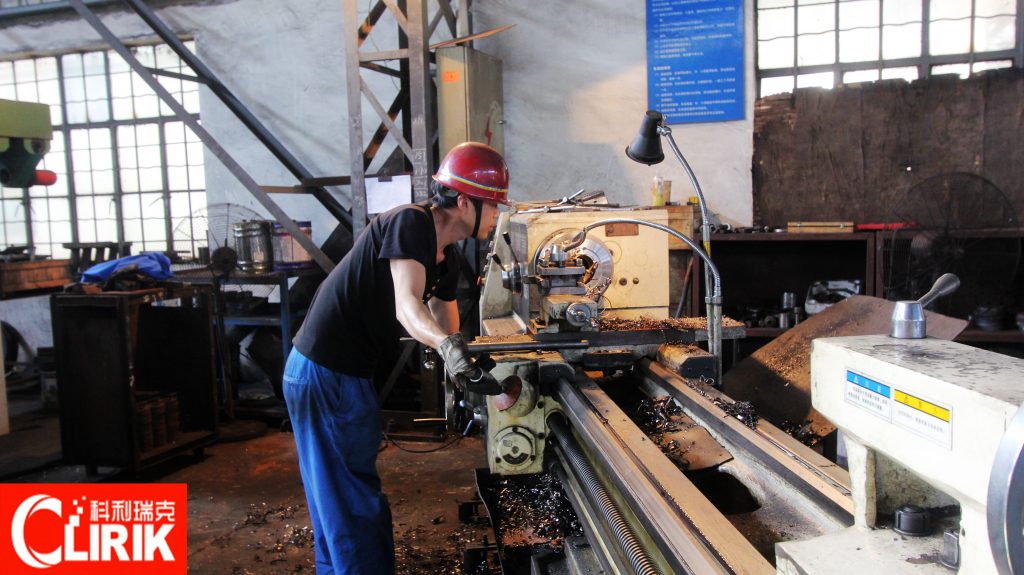
In the micro-powder grinding chamber, the grinding roller assembly is suspended on the grinding roller hanger through a cross arm. The grinding roller hanger is fixedly connected to the main shaft and the blade holder. The pressure spring is tightly pressed against the bearing shaft of the grinding roller by the tension rod. On the outer end of the cantilever, the crossarm axis is used as the support point, and the grinding roller is pressed tightly against the inner surface of the grinding ring by the spring pressure. When the motor rotates through the transmission device, the blade and grinding roller mounted on the blade holder Rotate synchronously.
HOT PRODUCTS
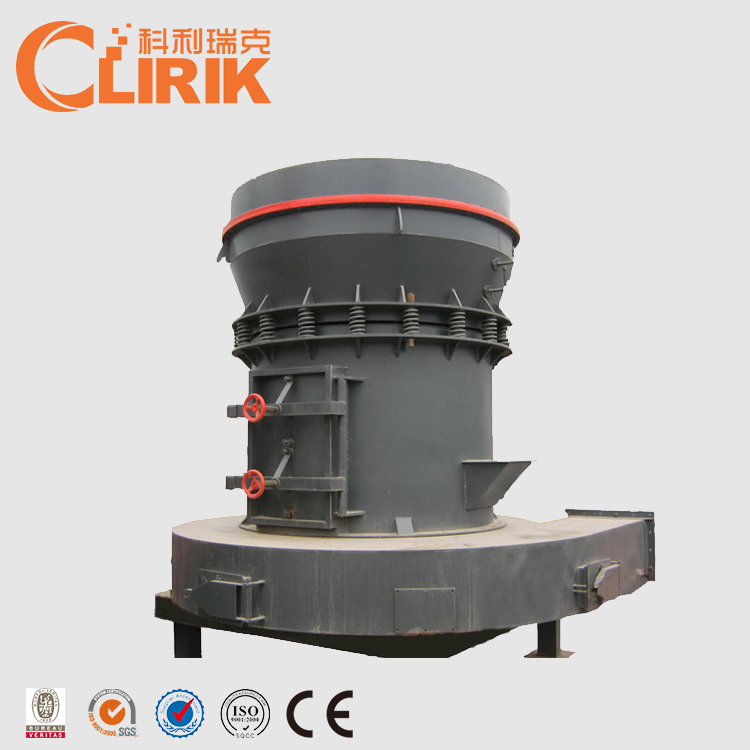
Talc Raymond Mill
Capacity: 1-25 t/h
Max feeding size: 40 mm
Discharge fineness: 50-325 mesh
Range of application: Barite, calcite, potassium feldspar, talc…… [Read More…]
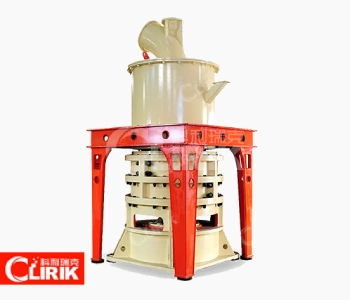
Micro Powder Grinding Mill
Capacity: 0.2-45 t/h
Max feeding size: 20 mm
Discharge fineness: 150-3000 mesh
Range of application: calcium carbonate, kaolin, carbon black, dolomite…… [Read More…]
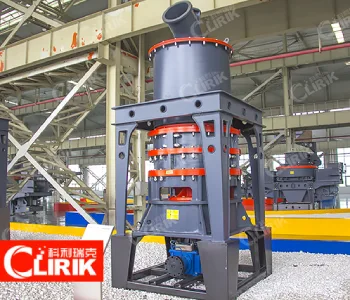
Talc Ultrafine Grinding Mill
Capacity: 0.2-45 t/h
Max feeding size: 20 mm
Discharge fineness: 150-3000 mesh
Processing materials: non-flammable and explosive non-metallic ores with Mohs hardness less than 7…… [Read More…]
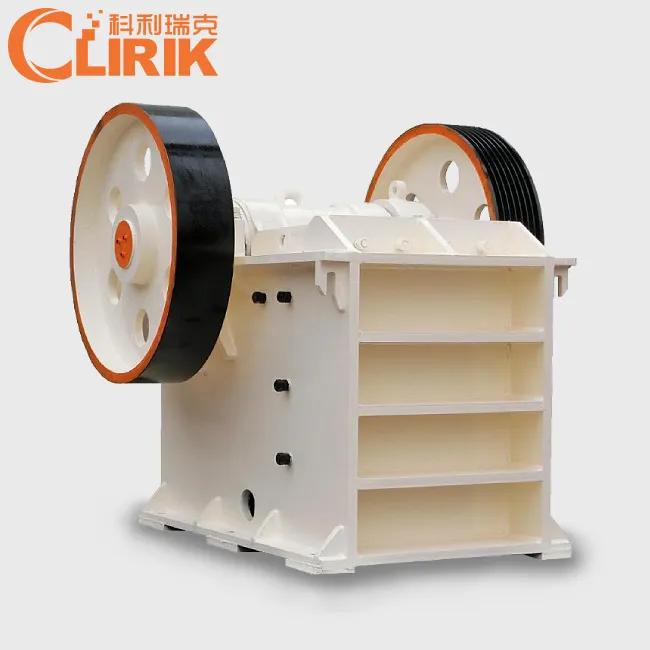
Talc Jaw Crusher
Output Size: 65-160mm
Feed size: 480mm
Capacity: 1-140t/h
Processing materials: Granite, quartz stone, river pebble, calcite, concrete, dolomite…… [Read More…]
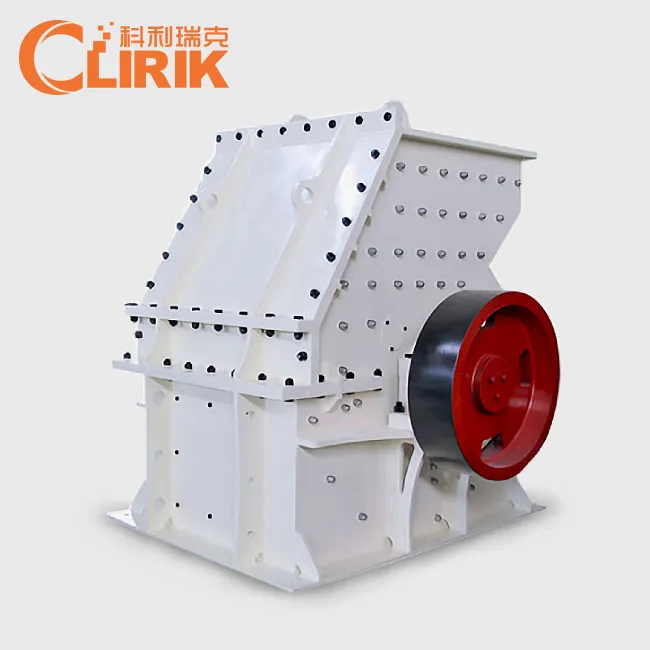
Talc Hammer Mill
Output Size: 5-20 mm
Feed size: <350 mm
Capacity: 5-30 t/h
Application: It is widely used for medium and fine crushing of brittle, medium hardness and soft materials... [Read More…]
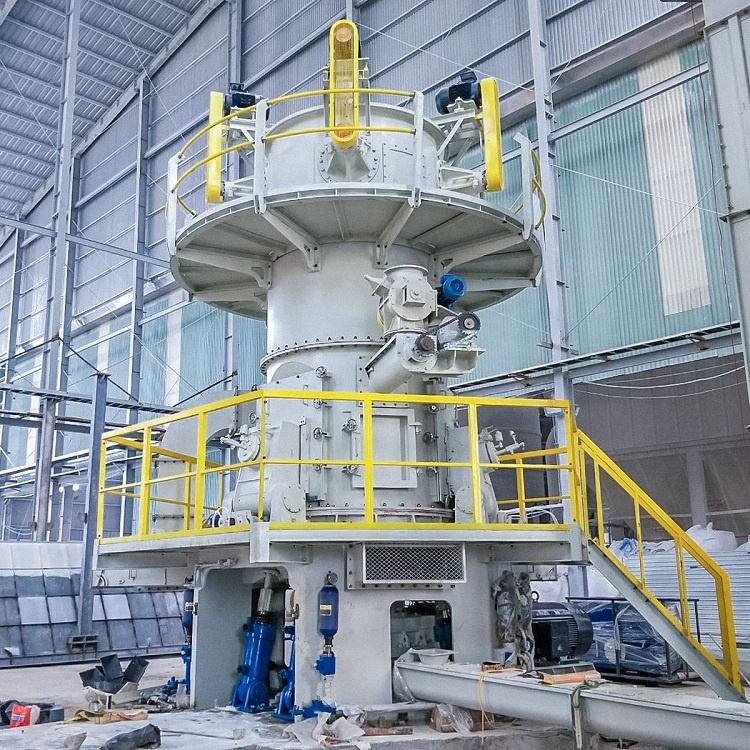
Talc Vertical Mill
Discharge fineness: 150-3000 mesh
Feed size: <15 mm
Output: 1-20 T/H
Product features: It has high grinding efficiency, low energy consumption, uniform particle shape... [Read More…]