Creating basalt rock dust involves several steps, primarily revolving around the crushing and grinding of basalt rock to a fine powder. Here's a step-by-step guide:
Step-by-Step Process:
Extraction:
Basalt rock is extracted from quarries or mining sites. Large blocks of basalt are typically broken down using controlled explosions or mechanical tools.
Primary Crushing:
The extracted basalt rock is transported to a primary crusher where large rocks are reduced to smaller, more manageable sizes. This can be done using jaw crushers.
Jaw Crusher
Secondary Crushing:
The smaller basalt pieces are further crushed in secondary crushers. Cone crushers, hammer crushers, or impact crushers can be used at this stage to achieve a finer particle size.
Cone Crusher
Hammer Crusher
Impact Crusher
Screening:
Crushed basalt is then screened to separate finer particles from larger fragments. This is done using vibrating screens with different mesh sizes to ensure uniform particle size.
Grinding:
The screened basalt is then ground into a fine powder using grinding mills. Various types of mills can be used, including:
Ball Mills: These grind the material by rotating a cylinder with steel grinding balls, causing the balls to fall back into the cylinder and onto the material to be ground.
Raymond Mills: Use rollers and a rotating bowl to pulverize the basalt.
Ultrafine Grinding Mills: Specifically designed to produce very fine powders, achieving particle sizes in the micrometer range.
Classification:
After grinding, the basalt dust is classified to ensure uniform particle size distribution. Air classifiers or sieves are used to separate fine particles from coarser ones.
Packaging:
The final basalt rock dust is packaged for distribution. It can be packed in bags, bulk containers, or other suitable packaging depending on the intended use and market requirements.
Equipment Used:
l Primary Crushers: Jaw Crusher, Gyratory Crusher
l Secondary Crushers: Cone Crusher, Hammer Crusher, Impact Crusher
l Grinding Mills: Ball Mill, Raymond Mill, Ultrafine Grinding Mill
l Screening Equipment: Vibrating Screens
l Classification Equipment: Air Classifiers, Sieves
Safety and Environmental Considerations:
l Dust Control: Implement dust suppression measures such as water sprays and dust collection systems to minimize airborne dust during crushing and grinding.
l Personal Protective Equipment (PPE): Operators should wear protective gear such as masks, gloves, and goggles to protect against dust exposure.
l Environmental Impact: Ensure that the process complies with environmental regulations regarding dust and noise pollution, and manage waste materials responsibly.
Creating basalt rock dust involves a series of mechanical processes that require specialized equipment to ensure the production of high-quality, finely ground basalt suitable for use in agriculture, construction, and other applications.
HOT PRODUCTS
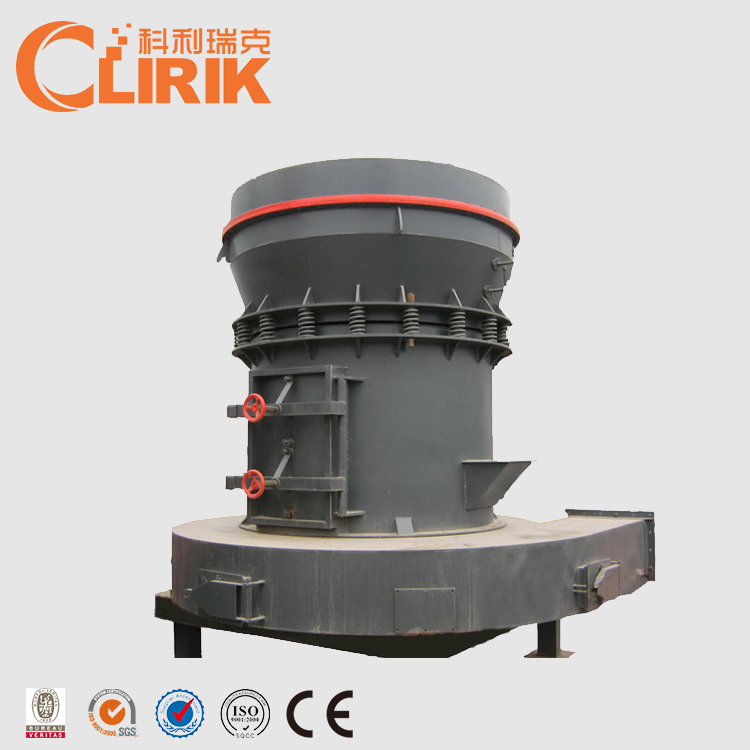
Talc Raymond Mill
Capacity: 1-25 t/h
Max feeding size: 40 mm
Discharge fineness: 50-325 mesh
Range of application: Barite, calcite, potassium feldspar, talc…… [Read More…]
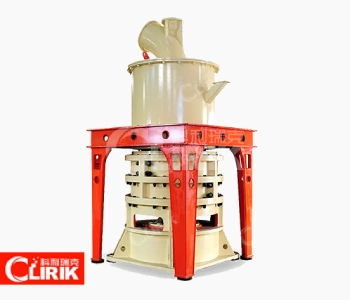
Micro Powder Grinding Mill
Capacity: 0.2-45 t/h
Max feeding size: 20 mm
Discharge fineness: 150-3000 mesh
Range of application: calcium carbonate, kaolin, carbon black, dolomite…… [Read More…]
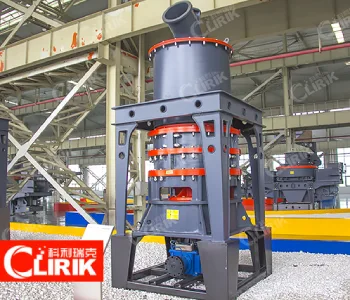
Talc Ultrafine Grinding Mill
Capacity: 0.2-45 t/h
Max feeding size: 20 mm
Discharge fineness: 150-3000 mesh
Processing materials: non-flammable and explosive non-metallic ores with Mohs hardness less than 7…… [Read More…]
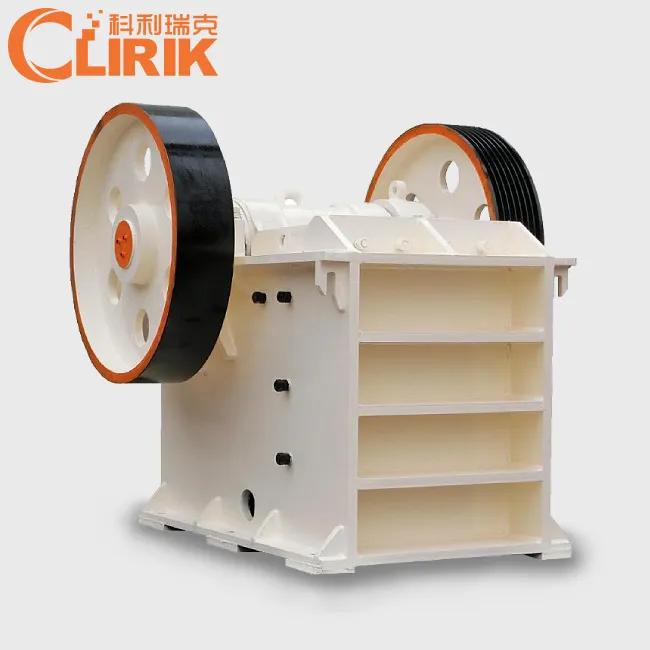
Talc Jaw Crusher
Output Size: 65-160mm
Feed size: 480mm
Capacity: 1-140t/h
Processing materials: Granite, quartz stone, river pebble, calcite, concrete, dolomite…… [Read More…]
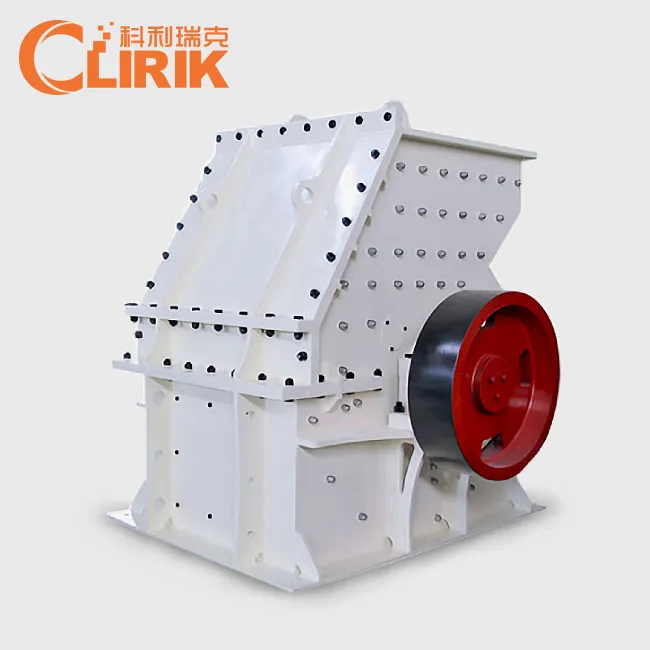
Talc Hammer Mill
Output Size: 5-20 mm
Feed size: <350 mm
Capacity: 5-30 t/h
Application: It is widely used for medium and fine crushing of brittle, medium hardness and soft materials... [Read More…]
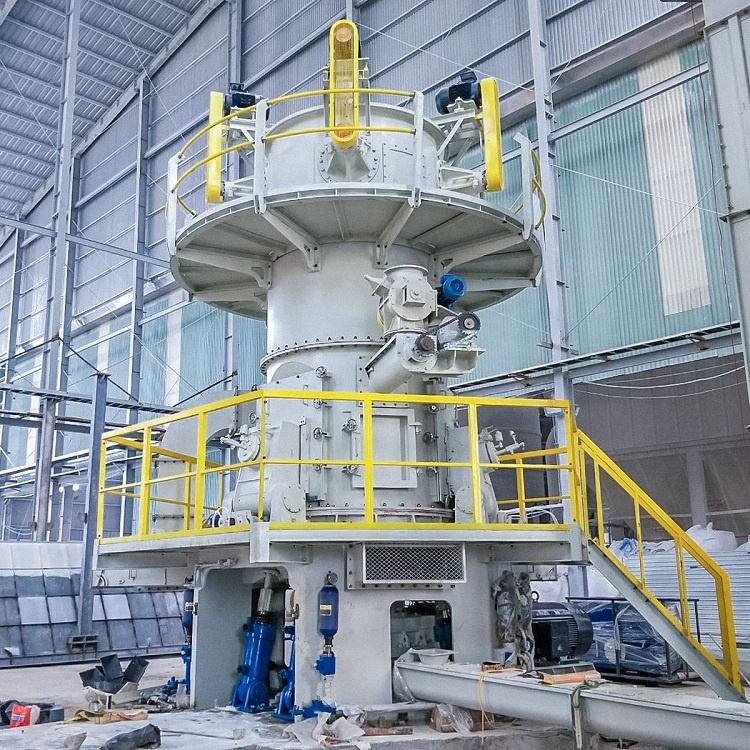
Talc Vertical Mill
Discharge fineness: 150-3000 mesh
Feed size: <15 mm
Output: 1-20 T/H
Product features: It has high grinding efficiency, low energy consumption, uniform particle shape... [Read More…]