The magnesium oxide grinding process is mainly divided into the following steps:
Raw material crushing: crush magnesium oxide blocks into small pieces less than 10mm to facilitate subsequent grinding processing. Commonly used crushing equipment includes jaw crusher, impact crusher, etc.
Coarse grinding: The crushed magnesium oxide pieces are further ground into fine powder. Grinding equipment such as Raymond mill and ball mill are generally used.
Fine grinding: According to the particle size requirements of the product, the magnesium oxide powder after coarse grinding is finely ground. Commonly used fine grinding equipment include ultra-fine grinding, airflow grinding, etc.
Classification: Classify the ground magnesium oxide powder to remove unqualified particles. Commonly used classification equipment include vibrating screens, air classifiers, etc.
Packaging: Pack the qualified magnesium oxide powder before leaving the factory for sale.
Grinding equipment
Commonly used equipment for magnesium oxide grinding include the following:
Raymond mill: It is a relatively traditional grinding equipment, suitable for grinding medium hard materials, such as magnesium oxide, limestone, cement, etc. The output of Raymond mill is higher, but the grinding fineness is lower, generally between 30-200 mesh.
Ball mill: It is a general grinding equipment, suitable for grinding materials of various hardness, such as magnesium oxide, quartz, ceramics, etc. The crushing fineness of the ball mill is adjustable, generally between 80-325 mesh.
Ultra-fine grinding mill: It is a new type of grinding equipment, suitable for grinding materials with high hardness and high viscosity, such as magnesium oxide, calcium carbonate, titanium dioxide, etc. The crushing fineness of ultra-fine grinding can reach more than 1000 mesh.
Airflow mill: It is a device that uses airflow for crushing. It is suitable for grinding materials with high fineness requirements, such as magnesium oxide, pigments, medicines, etc. The grinding fineness of airflow mill can reach below 10 microns.
Production line advantages
Magnesium oxide grinding production line has the following advantages:
The process is mature, the production efficiency is high, and the product quality is stable.
Reasonable equipment selection, low energy consumption and low operating costs.
High degree of automation, simple operation and easy maintenance.
It has good environmental performance and low dust emission.
The magnesium oxide grinding process is mature, the equipment selection is reasonable, and the production line has obvious advantages. It is an ideal choice for the production of magnesium oxide powder.
HOT PRODUCTS
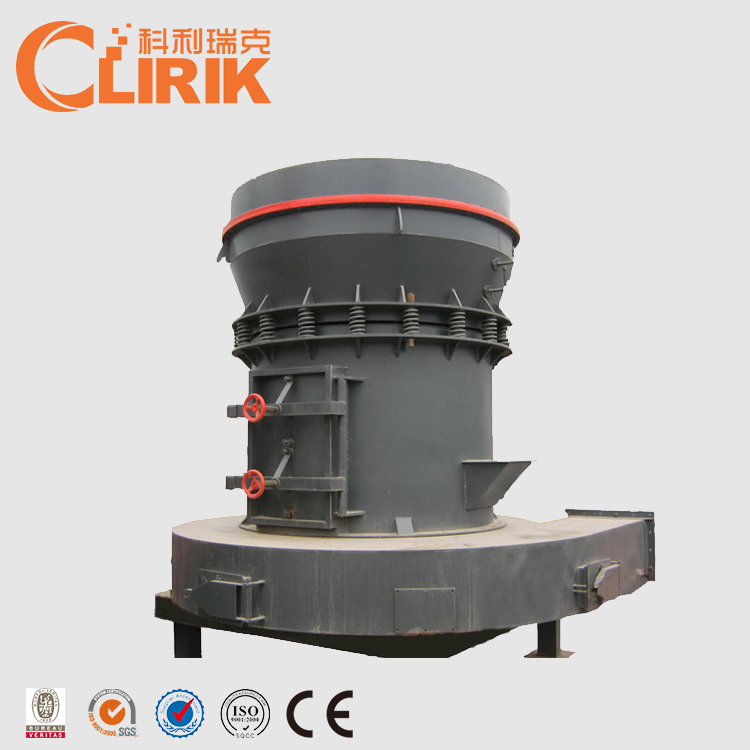
Talc Raymond Mill
Capacity: 1-25 t/h
Max feeding size: 40 mm
Discharge fineness: 50-325 mesh
Range of application: Barite, calcite, potassium feldspar, talc…… [Read More…]
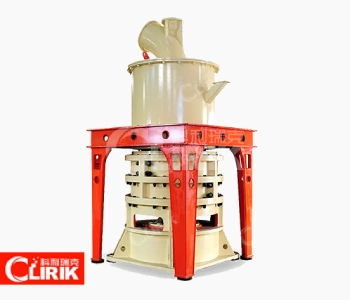
Micro Powder Grinding Mill
Capacity: 0.2-45 t/h
Max feeding size: 20 mm
Discharge fineness: 150-3000 mesh
Range of application: calcium carbonate, kaolin, carbon black, dolomite…… [Read More…]
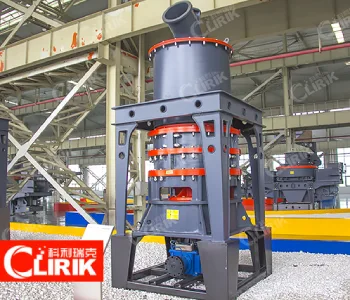
Talc Ultrafine Grinding Mill
Capacity: 0.2-45 t/h
Max feeding size: 20 mm
Discharge fineness: 150-3000 mesh
Processing materials: non-flammable and explosive non-metallic ores with Mohs hardness less than 7…… [Read More…]
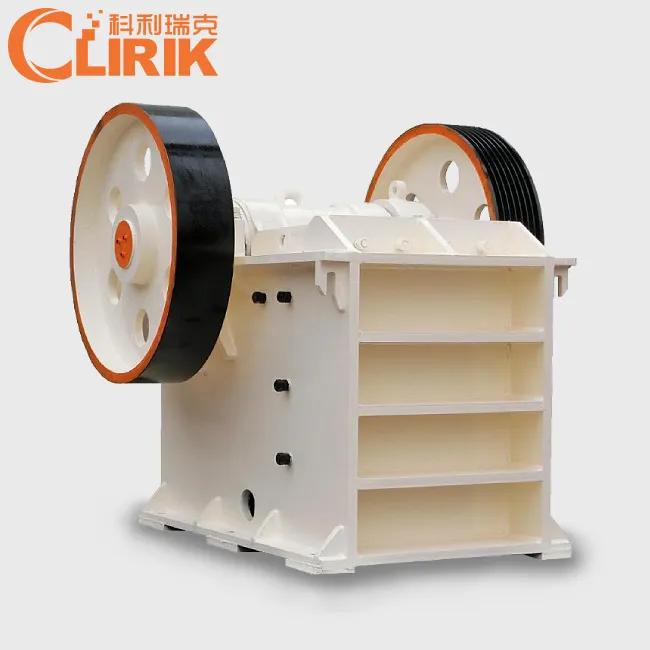
Talc Jaw Crusher
Output Size: 65-160mm
Feed size: 480mm
Capacity: 1-140t/h
Processing materials: Granite, quartz stone, river pebble, calcite, concrete, dolomite…… [Read More…]
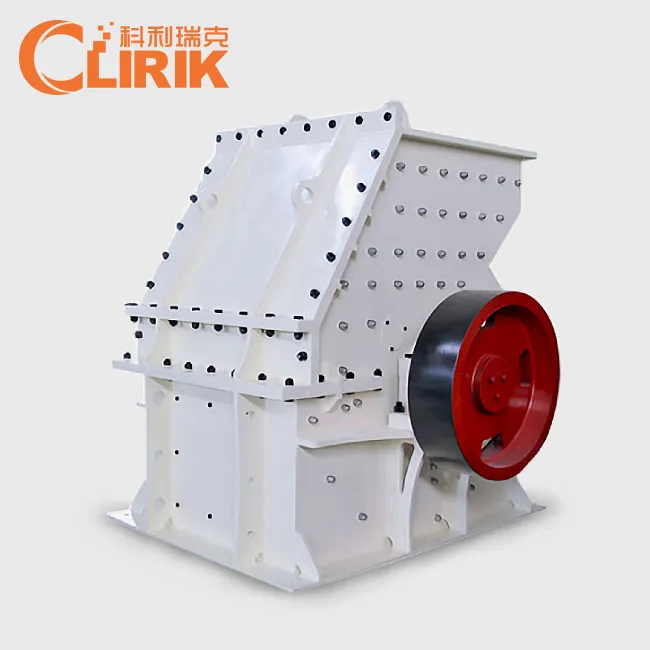
Talc Hammer Mill
Output Size: 5-20 mm
Feed size: <350 mm
Capacity: 5-30 t/h
Application: It is widely used for medium and fine crushing of brittle, medium hardness and soft materials... [Read More…]
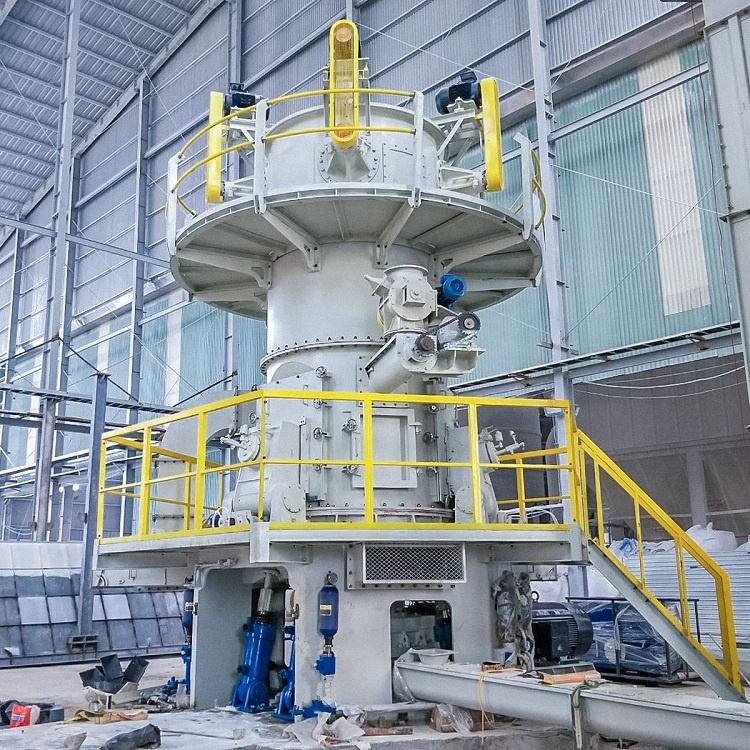
Talc Vertical Mill
Discharge fineness: 150-3000 mesh
Feed size: <15 mm
Output: 1-20 T/H
Product features: It has high grinding efficiency, low energy consumption, uniform particle shape... [Read More…]